Our Team memebers
Our team is composed of three Mechanical Engineering students who have all grown up in California.
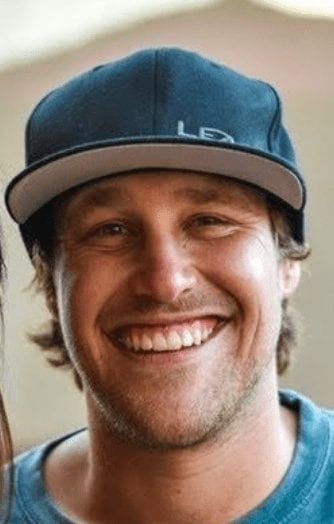
Colton Arbuckle
Team Organizer/lead Builder
I am a forth year Mechanical Engineer with a general concentration. I am an avid outdoorsman and cyclist who grew up in San Luis Obispo. For 7 years I’ve worked at local bicycle accessory manufacture as a test technician working my way through school. Throughout high school I found the love for wrenching on anything with wheels, which ultimately lead me to pursue Mechanical Engineering as a career.
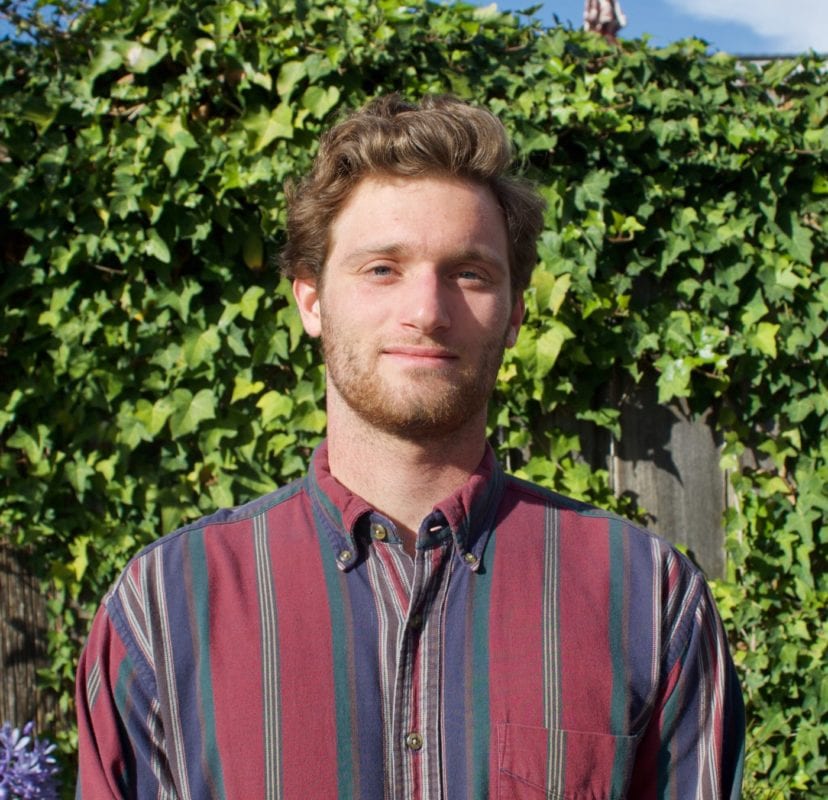
Chris Menke
Sponsor communications Leasion
I enjoy spending time outside and have an interest in thermodynamics and heat transfer. I will be working in the HVAC industry once I graduate.
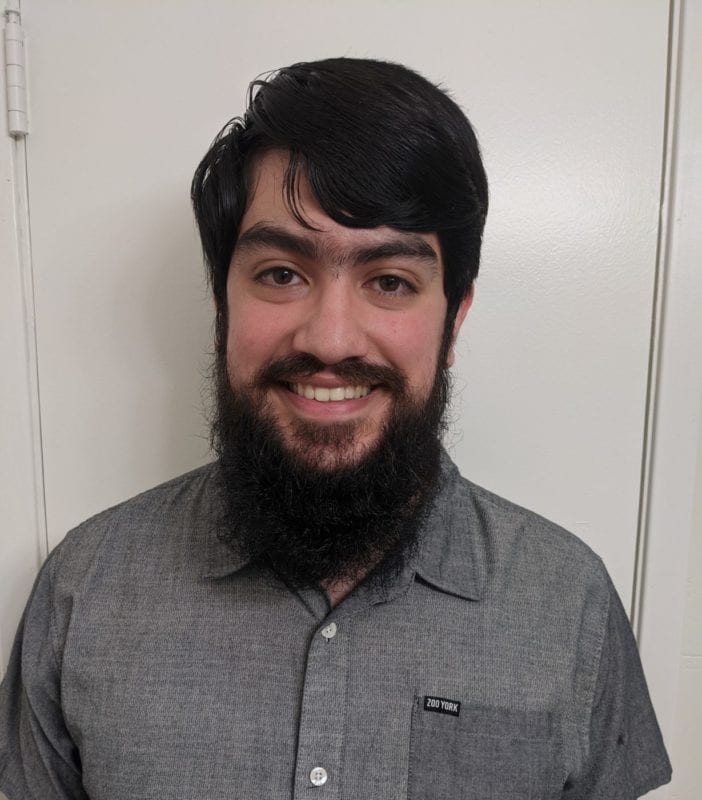
Jacob Rodriguez
video editor/cad designer
I enjoy taking hikes in the mountains and doing sports, mostly soccer and wrestling. I am hoping to work in the field of prosthetics.
Acknowledgements
- The SoleMates team wanted to say thank you to:
- Trevor Harding, the Materials Engineering Department Chair, for allowing us to use the PosiTest AT-M equipment to test adhesive properties.
- Meredith Ruben, for working with us in assisting with purchase orders.
- Sarah Harding, our Sr. Project Advisor, for continuous support and guidance.
- Dana Cummings, our Sponsor, for insight and assistance throughout testing
Our Project's Videos
Our Project's Digital Poster
Problem Statement
- Dana Cummings is a marine veteran who uses a lower leg prosthetic and various types of different foot shells.
- Foot shells are attachments for prosthetic feet that allow the user to wear shoes and decrease the wear on their prosthetic.
- Our sponsor needs a design that can withstand rigorous use because he is more active than the typical user.
- Our team was tasked to design a product that extends the life of silicone-style prosthetic foot shells while keeping cost as low as possible.
FAILURE MODES
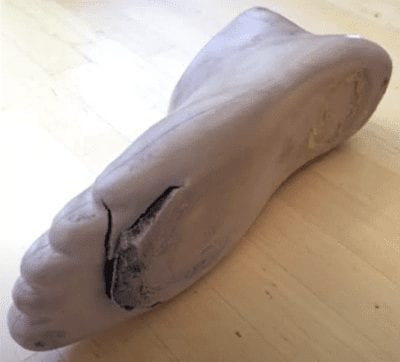
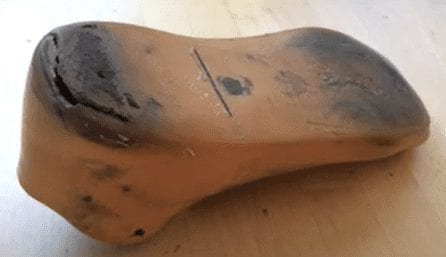
Typically silicone style foot shells fail in the toe and heel sections of the shell from the carbon fiber prosthetic stabbing through. The design of prosthetics causes distributed forces to concentrate in these two locations.
Design Specifications
- -Withstand 300 lb Compressive load
- -Less than $15
- -Less than 8 oz
- -Flexible to 15°
- -Withstand 160°F heat
Iterative Design Process
Build, Test, Prototype:
The team utilized an iterative design process in creating this product along with rapid prototyping.
This style of design utilizes readily available materials and multiple iterations throughout the design process which is highlighted throughout the alternate designs section.
The team conceptualized, idealized, and functionally tested each iteration on pass fail criteria. Which can be seen through out our report.
CAD Rendering
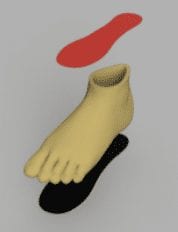
Rendered CAD model of insole and external SoleMates
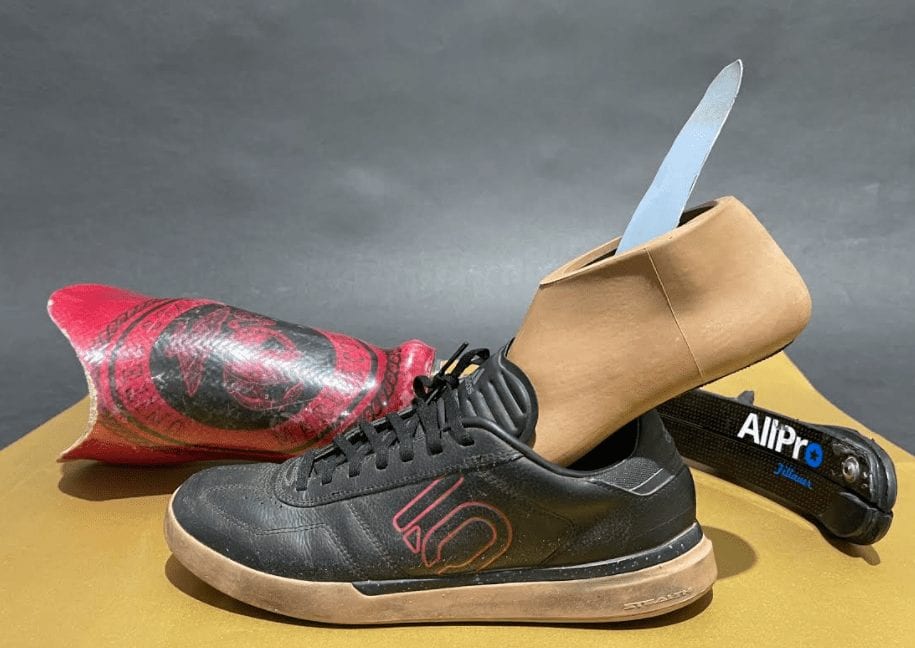
Recommendations
Since the real-world test proved that barge cement failed to keep the external sole adhered. The team jumped in to the next iteration of using a two-part epoxy. This two-part epoxy has initially passed the insertion/reinsertion test that simulates the shell being used as the intended end consumer would.
The next step would be putting this combination through the real-world test. If this adhesive would prove to fail the team would go back to the drawing board and implement cyanoacrylate accelerators into the equation. These accelerators that are applied to the bonding surfaces before the adhesive allows for a very quick bonding of materials. These type of accelerators are useful to cure different types of adhesives that have the possibility of being pressed out of the two substrates when placed together to cure.
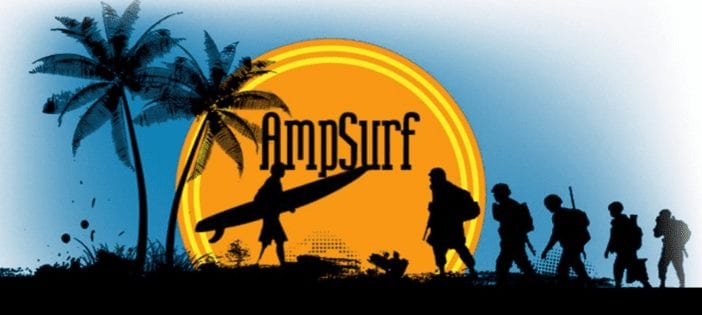
This project is sponsored by AmpSurf™
Early Testing
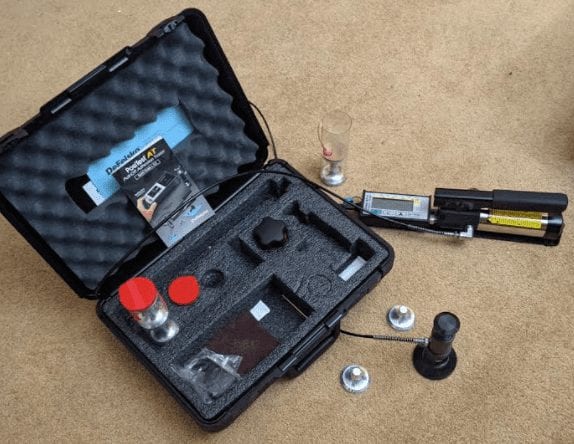
The Positest AT-M is a Hydraulic Adhesion Testing machine which is how the team selected the adhesive to be used on the external sole.
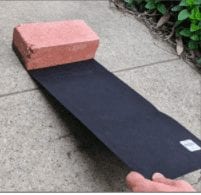
The team tested durability of different soling materials by placing a 10 lb brick on them and dragging them across a 10 foot section of concrete.
Test Results
When choosing an adhesive we tested on many different materials. Some data from initial trials can be seen below.

Once we decided on Barge cement for the adhesive, we did further testing on thermoplastic. We then did uncertainty analysis with this data.
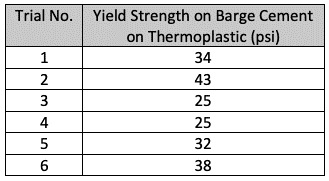
After doing uncertainty analysis with this data we found that the barge cement had a yield strength of 32.7±7.7 psi
Verification Testing
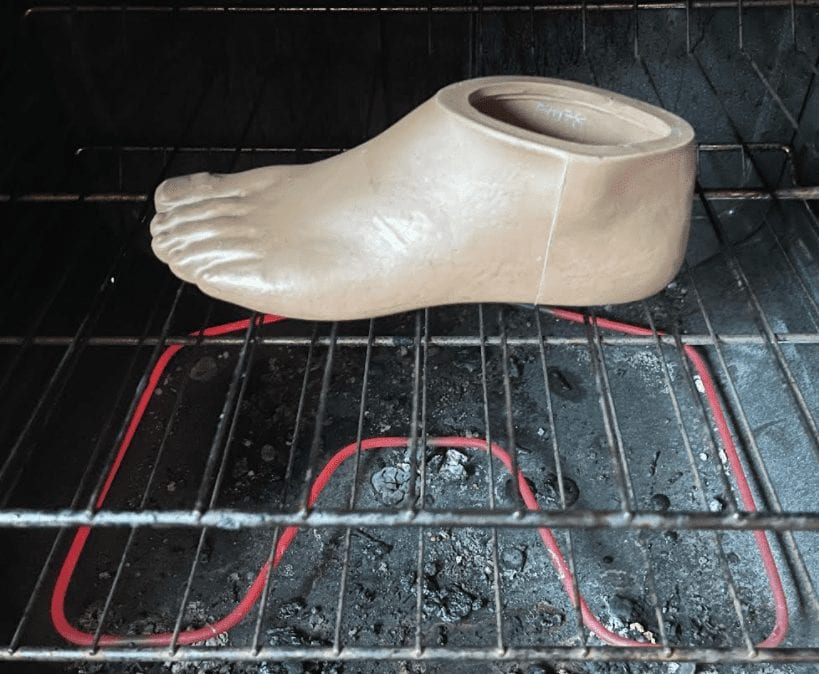
Heat Test –The prototype must be resistant to temperatures up to 160° F, which it could be subject to on a hot summer day if left in a car.
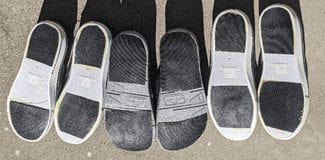
Shoe Test – Our design was verified by using and applying the soling material and adhesive to the bottom of each team members shoes. This test applied the dynamic conditions that the external sole and adhesive would see throughout the life of the shell. The rubber soles lasted on all 6 shoes from early march to June with regular use.
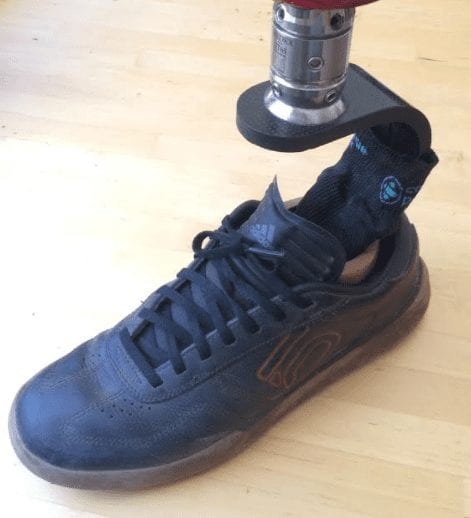
Insertion/Reinsertion Verification –This product is continuously being put on and taken off. The team verified that this design would uphold to 365 times into and out of a shoe. Simulating the intended use of the product in the same manner that it will see.
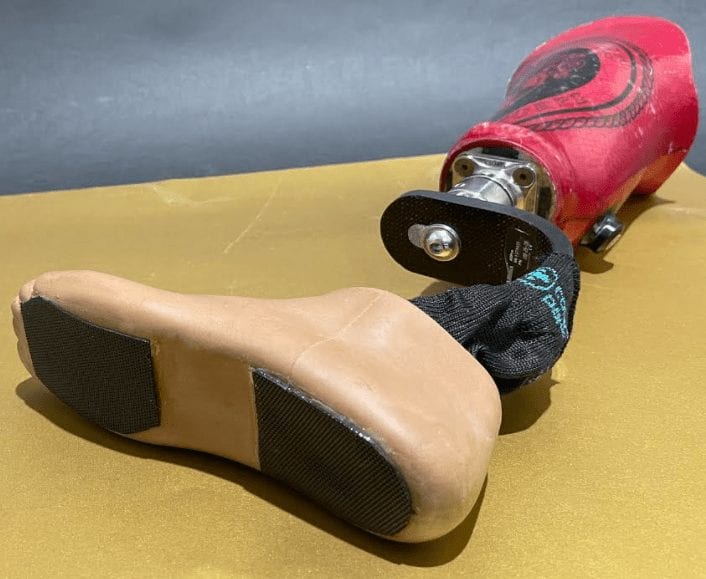
Dana Real world test- In order for the design to be solidified. Our Sponsor had to ultimately provide real world test results for the team.
Final Design
Our Final Design is a DIY kit that any prosthetic user can implement into their shell to make it more robust. The external rubber sole has been adhered with barge cement, and the insole is made of high density Polyethylene.
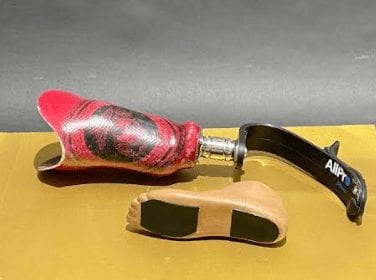
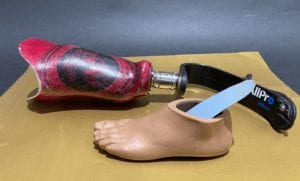
Included In Kit
- -High Density Polyethylene (HDPE) insole
- -Barge Cement
- -External Soling rubber
- -Gloves
- -Electrical Tape
Not Included In Kit
- -Scissors
- -Prosthetic
- -Rubbing Alcohol
- -Foot Shell
- -Sharpie
- -Paper Towels
Alternate Designs
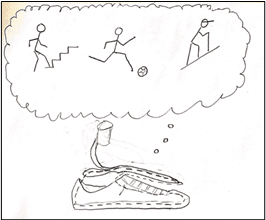
This boundary diagram is drawn to show that this design is for active individuals. Within this design one must consider the type of prosthetic that will be used in conjunction with the foot shell itself.
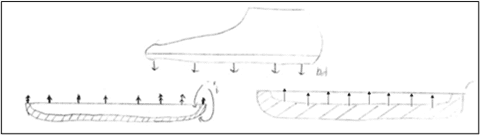
Another system is called the “Repairable.” It would be a foot shell with interchangeable soles. Once one of the soles wears through, the user could switch out just the sole, while keeping the rest of the foot shell. This lead the team to entertain the idea of having different sole attachments for different levels of activity.
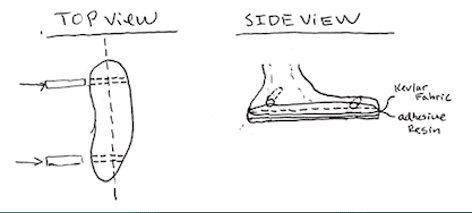
One of the other designs brainstormed by the team during ideation was called pin fixed. This is because it uses pins to prevent motion between an interior sole and the prosthetic.
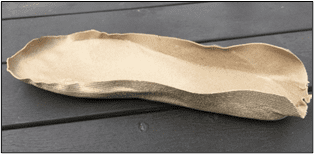
This idea was a custom molded thermoplastic insole.
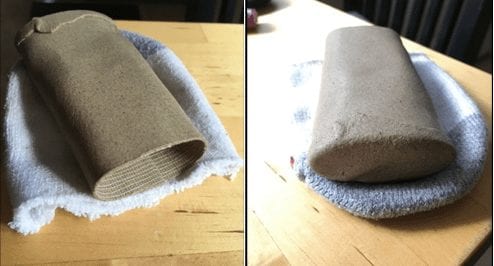
Prosthetic shell users wear a special sock to protect wear on their prosthetic. The team wanted to think of a solution that helped relieve wear on both the prosthetic and the prosthetic foot shell. This is a Thermoplastic co-molded sock.