Our Team
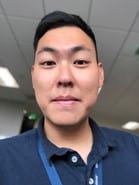
Jung Kim
Team manager
My name is Jung Sub Kim (I go by Jung with a J- not Y- pronunciation). I am currently staying at Fullerton, CA. I am pursuing to become a fire protection engineer after I receive my bachelor’s degree. Besides my personal goal, I would like to contribute to our project to extend the mechanical design skillsets I received to an actual practical application.
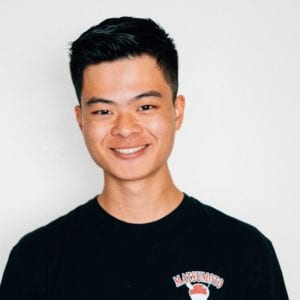
David Yang
Documentation / Manufacturing
Hey, my name is David Yang! I’m from Irvine, CA and my concentration is General. I’m most interested in vehicle dynamics and manufacturing. Apart from schoolwork, I love to be outside – hiking, trail running, and rock climbing are all in my repertoire. I also love working on cars!
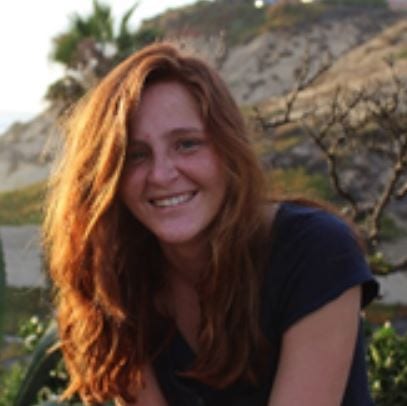
Team Member
attache / manufacturing
Hi! I’m Ellie Kitabjian and I’m a fourth year Mechanical Engineering student from San Diego, California. I am interested in Space Systems Engineering and satellite design. When I’m not working I like to play soccer and go for runs.

Team Member
Treasurer
Hello, my name is Christopher Macias and I’m from Fresno, CA. In general, my interest in mechanical engineering is in being able to design something that has a purpose. It’s always satisfying to see your work coming together into a functional system.
Acknowledgements
Special Thanks to our sponsor/coach, Peter Schuster and Sarah Harding, and also to CPConnect Funding.
Problem Statement
Existing collaborative tables lack the key combination of transportability, compact storage, surface quality, and durability for group projects. College students need an ergonomic, multifunctional table unit capable of supporting all levels of interactive work, from one-on-one tutoring to large group prototyping sessions to maximize productive time in a busy day.
Design Constraints
- Compact Storage – Four tables shall fit in a footprint no larger than 1.5x its stacking direction.
- Table Height – Minimum of 30 in.
- Deployment Time – Maximum of 30 seconds.
- Fold Time – Maximum of 45 seconds.
- Cost – Maximum of $350.
- Tipping load – Withstand 125 lb. at edge.
- Concentrated Load – Withstand 200 lb.
- Drop Test – Endure drop from 2.4 in.
- Leg Strength – Withstand 100 lb.
Existing Design
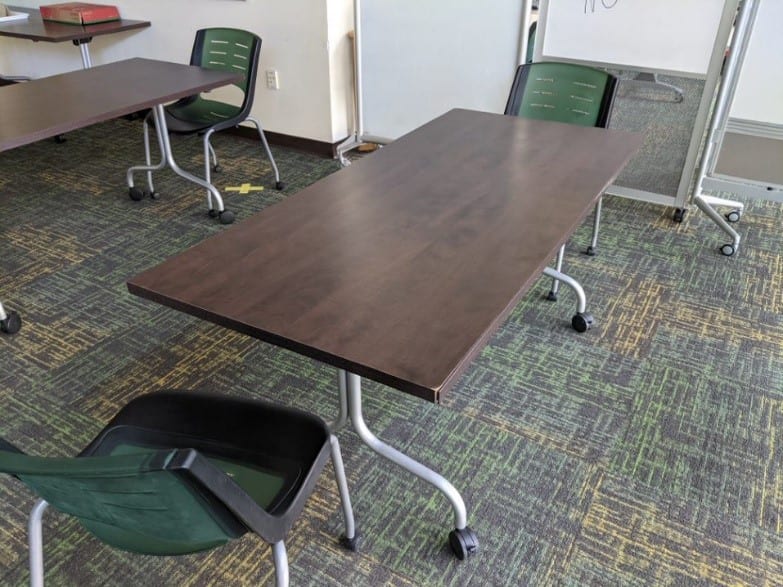
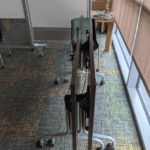
The major problem of the existing single-axis folding table is the shakiness and wobble caused from the hinge system. The stacking efficiency (Ratio of Single table foot print to the footprint of two stacked tables) is 76%.
Initial Sketch
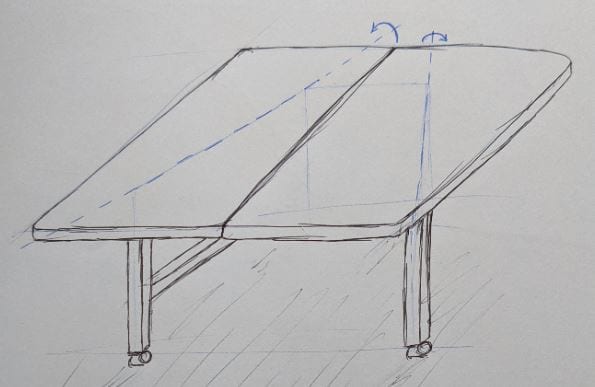
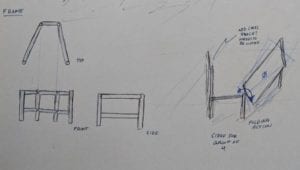
A trapezoidal base promotes compact nesting, and the center-split table allows for fast deployment and folding. Our initial concern was the dimensions of the trapezoidal frame since increasing its size limits the stacking efficiency.
Design Analysis
Stacking efficiency
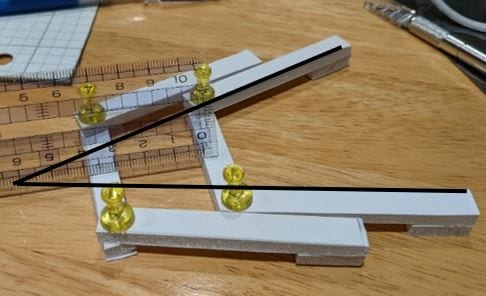
Base Angle Study
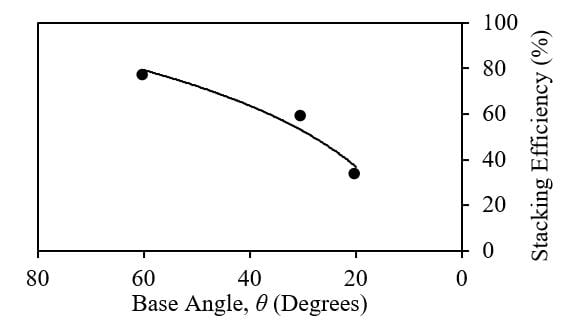
Finding the Optimal Base Angle for Maximum Stacking Efficiency
The figure on the left demonstrates the base angle dimension shown with black lines on the mock up trapezoidal table frame. The right side figure shows the relationship of base angle to the stacking efficiency (Ratio of Single table foot print to the footprint of two stacked tables) derived from CAD model study. The greater the base angle, the greater the stacking efficiency. Our final table design has a base angle of 36°, and stacking efficiency of 78%
load / tipping analysis
Trapezoid frame dimensions was optimized using an excel spreadsheet calculations. Above figure shows the diagram that was used for the calculation. Major constraint of the frame was to resist tipping, and optimization process was a compromise among the Stacking efficiency, Overall weight (Pipe Thickness), and the Tipping resistance.
UHMWPE Bushing Wear analysis
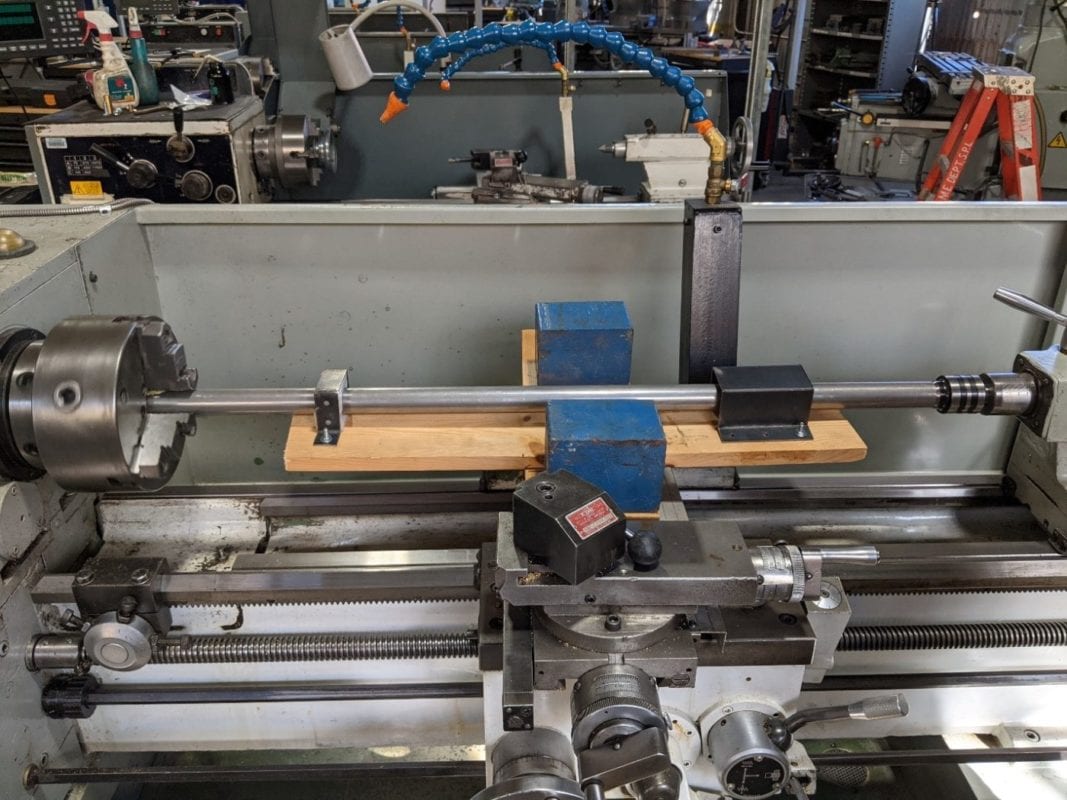
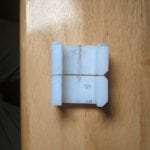
We conducted a wear test of UHMWPE bushing by spinning a steel pipe along the assembled bushing with a lathe, which helped us to find a set of optimal bushing dimensions and tolerances.
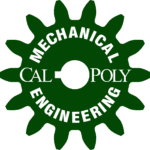
This project is sponsored by Dr. Peter Schuster of Cal Poly San Luis Obispo Mechanical Engineering department and also by CPConnect.
Final Design
Specifications
Weight -56 lbs Dimensions -55” X 48” X 31” Price – $348
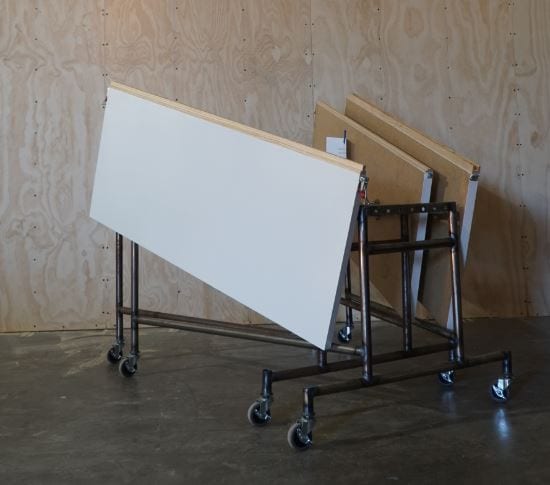
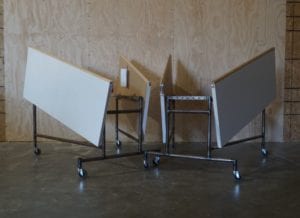
Custom Components
1.25″ Steel Pipe welded Frame
UHWMPE (Ultra high molecular weight polyethylene) Bushing
Steel Plate Bushing Carrier
Hardwood Tongue and Groove
Stock Components
2X IKEA LAGKAPTEN (55x24x1.4)
4X Caster Wheels
1X Compression Latch
Anchor Hardware and screws
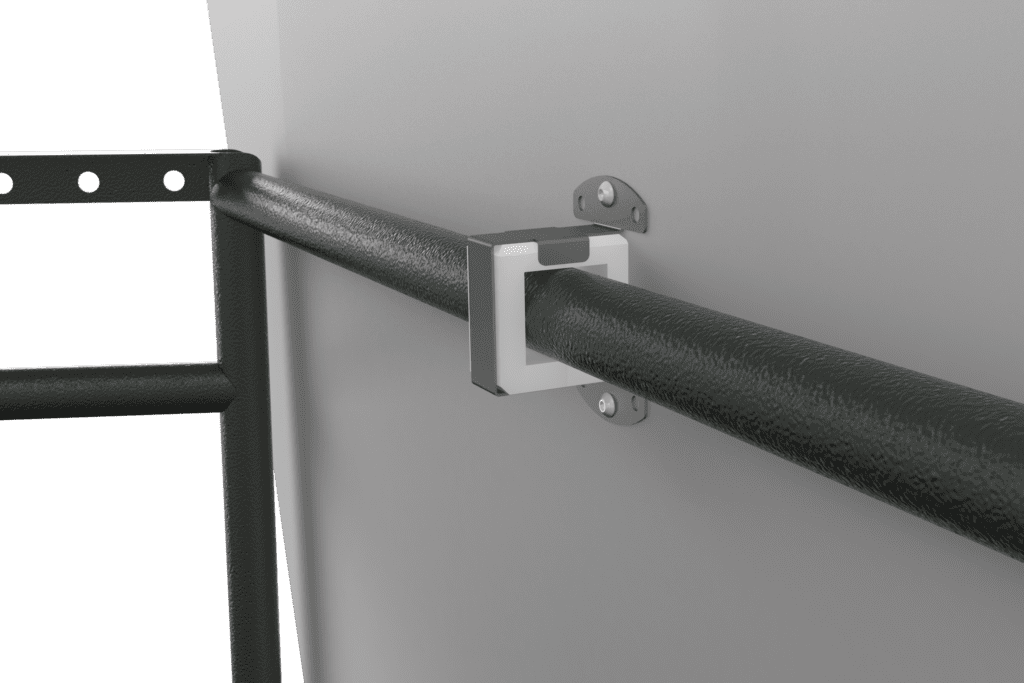
Two (2) Bushing subsystems join one (1) tabletop to the frame. The UHWMPE bushing smoothly slides and rotates along the frame, but provides enough friction so that the tabletop does not drop down when being folded.
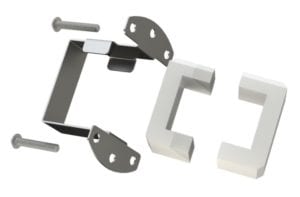
A bushing subsystem includes two pieces of matching UHMWPE milled bushings, a waterjet cut and folded steel plate bushing carrier, and six (6) screws – three on each side . The bushing carrier holds the bushing in place when in movement.
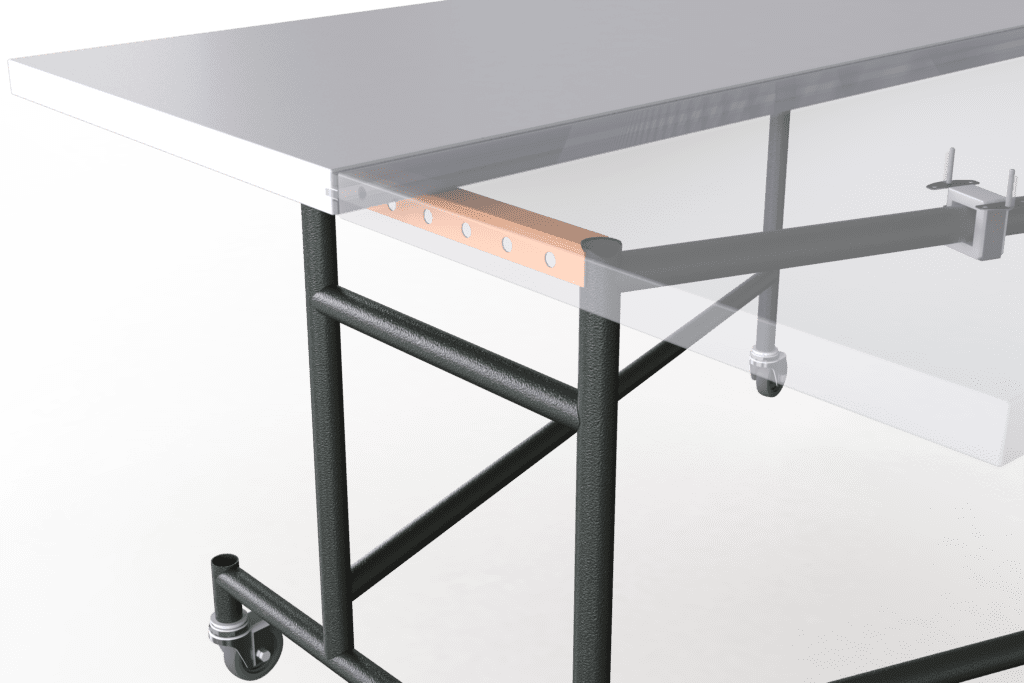
The bump stop subassembly is fixed to the frame to prevent over-rotation of the tabletops. It is made of steel plates, folded, and notched to be welded on the frame.
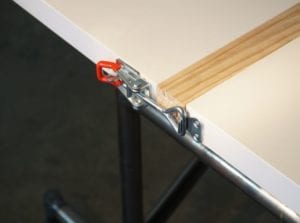
To hold the joining assembly in place, we installed a compression latch onto the sides of the table. This will aid the joining slots in bearing the loads.
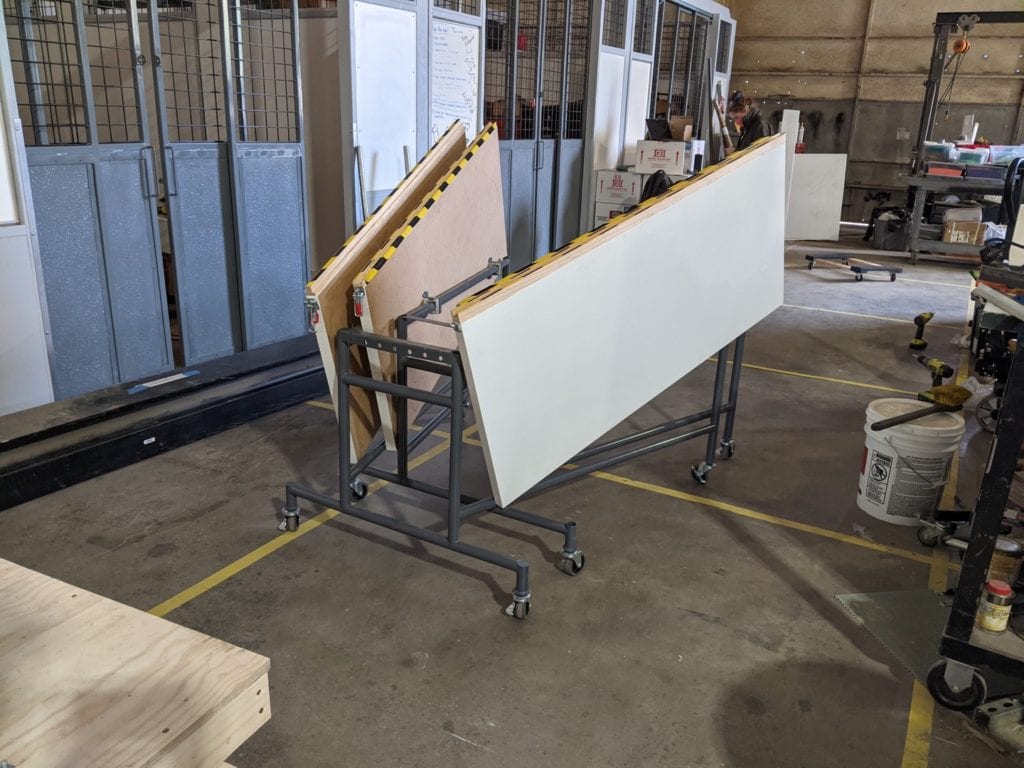
The tongue and groove feature created a pinch hazard when the table is being deployed. To prevent this hazard, black/yellow warning tape was applied across the feature.
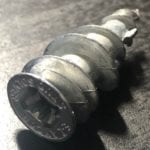
Drywall Anchors are installed on the surfaces of the tabletop to attach the hinge brackets and compression latches. Anchors allow multiple installs/reinstalls of the screws.
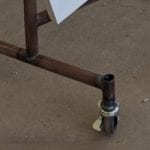
According to our tipping analysis, the trapezoid shape frame could not handle the design tipping load. To address this deficiency, outriggers were welded on the frame. Four (4) caster wheels were installed for ease of mobility.
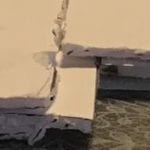
The horizontal extension (tongue) is shown on the left, and the horizontal slot (groove) is shown on the right. This feature guides the table deployment, as well as bears the vertical load.
Concept Design
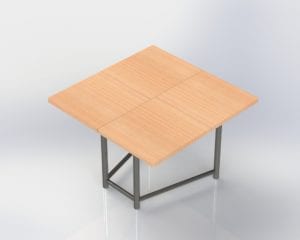
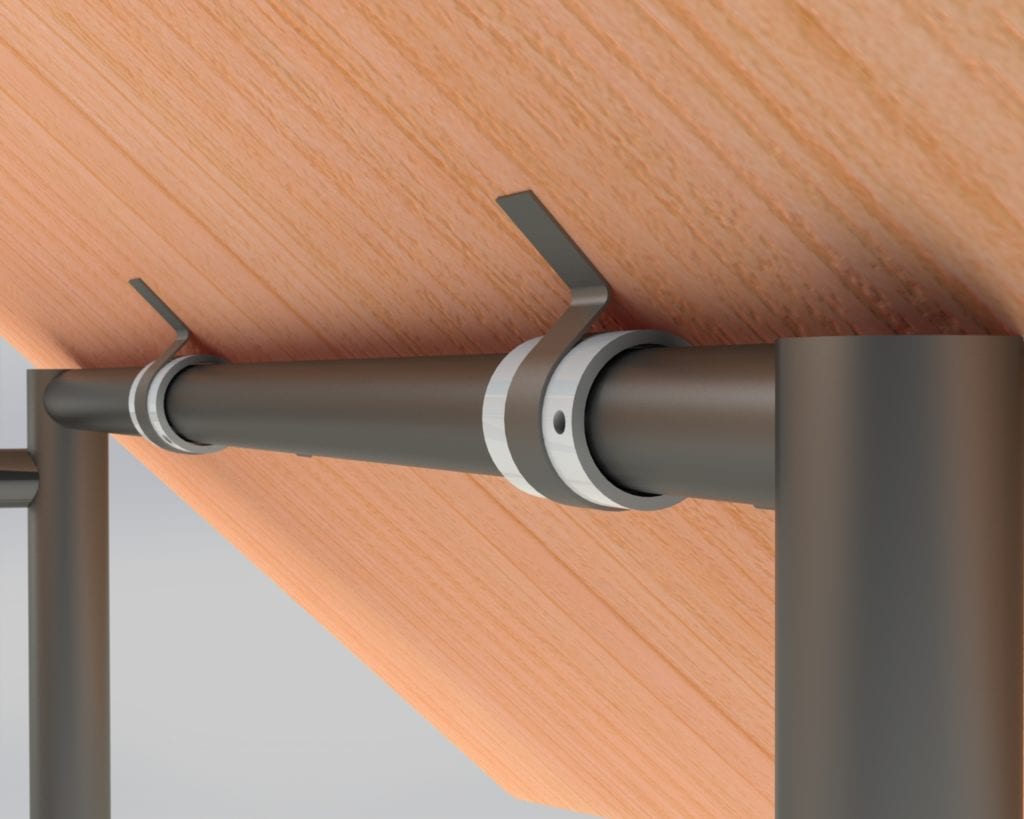
The initial Concept design of the hinge design was carried over to the final design. The initial design had circular PVC pipes which were replaced with UHMWPE four (4) point contact rectangular bushings.
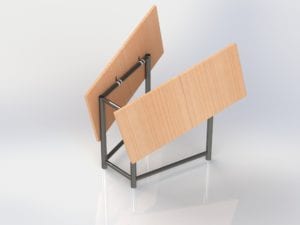
the concept CAD design of the table did include the finer details of the frame and table as a whole, but focused on the geometry of the frame as well as the ideations of the hinge.
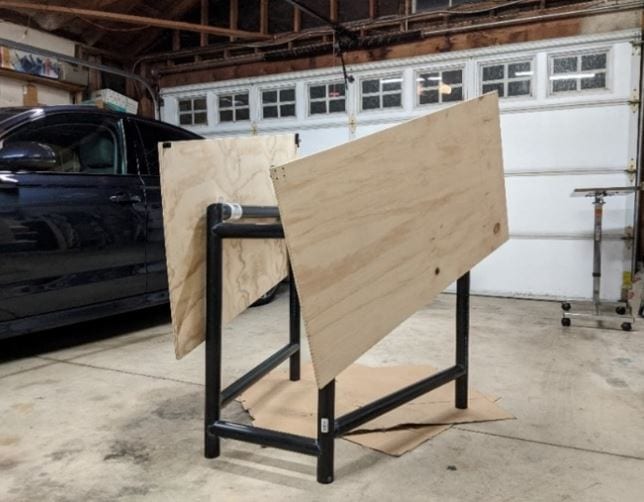
A concept prototype (1:1 scale) was made out of two (2) 12″x48″ plywood, ABS pipe frame, and PVC collar hinges.
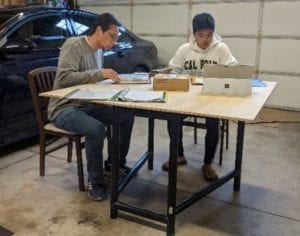
A preliminary usability test was performed on the concept prototype to experience the usage of the trapezoid-frame table and identify issues that needed correction.
Design Verification
Usability testing highlights
Deploy and Stow Test- Seven (7) participants without experience with the table were timed deploying and folding the table. The average deploy time was 34 seconds (Max 30 seconds in design criteria) and the average folding time was 33 seconds (Max 45 seconds in design criteria).
Stacking Efficiency Test- Measured the physical dimension of two tables stacked together to confirm the design stacking efficiency. Measurement showed approximately .5% increase in the actual storage foot print compare to the anticipated storage foot print.
Long Term Usage Test- From our internal usage test, we evaluated that 1) the bushing carrier heavily affected how the hinge sliding feels 2) the bump stop assembly was updated from a design with a potential pinch hazard to a pinch free design 3) we needed to install anchors on the tabletop edge for compression latch mating 4) the trapezoidal frame shape did not interfere user’s legs and 5) the tongue/groove lacked the anticipated vertical load support.
durability testing highlight
Statistical Bushing Carrier Manufacturing Test- We noticed from the long term usage test that the bushing dimensions (A and B) determined the fitting of the hinge to the frame pipe. By manufacturing multiple bushing carriers and testing out the fittings, we developed proper tolerances for the critical bushing carrier dimensions which will help benefit possible mass-manufacturing.
BIFMA (Business and Institutional Furniture Manufacturers Association) Tests- BIFMA offers design constraints for office tables, which include 1) 125 lb. maximum tipping load, 2) 200 lb. maximum concentrated Load, 3) 2.4 in height drop test, and 4) 100 lbs. minimum leg strength. Our verification prototype passed all the BIFMA required tests except the 200 lb. concentrated load (102 lb. actual), presumably due to the current tongue/groove feature design.
Hardware Compatibility Test- We tested multiple types of hardware on our special IKEA table top (Particle board shell with hex paper filling) to ease the subcomponent assembly process and also for future repair process. The tests included a weight drop test, creep test, and destructive test.
Recommendation
We recommend the further improvement of the tongue and groove feature which joins the tabletops together when in the deployed configuration. The design of that feature was the major reason we did not achieve the goal of supporting a concentrated load of 200 lbs. Other than the issue with the concentrated load, our fully built verification prototype was able to meet all the engineering specification we anticipated from the design as well as other criteria we had not previously defined, such as wobble-free hinges and repair-friendly tabletops equipped with anchor hardware.