The Team
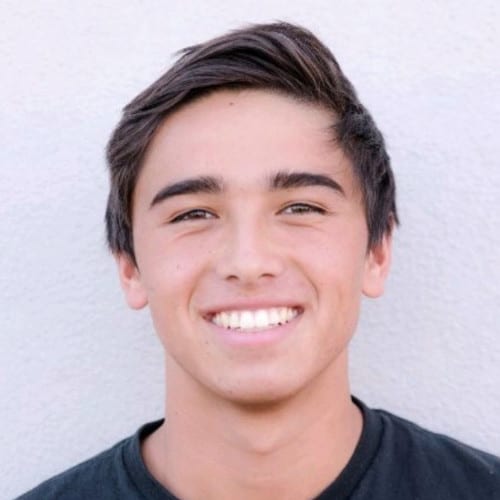
Peter Hunt
SPonsor Liason/Cad Lead
I am a 4th year Mechanical Engineering student from San Rafael, California. I will be pursuing graduate studies at the end of this year, and hope to start a career in the medical device industry upon graduation. I enjoy spending my free time outdoors, camping, fishing, or hiking.
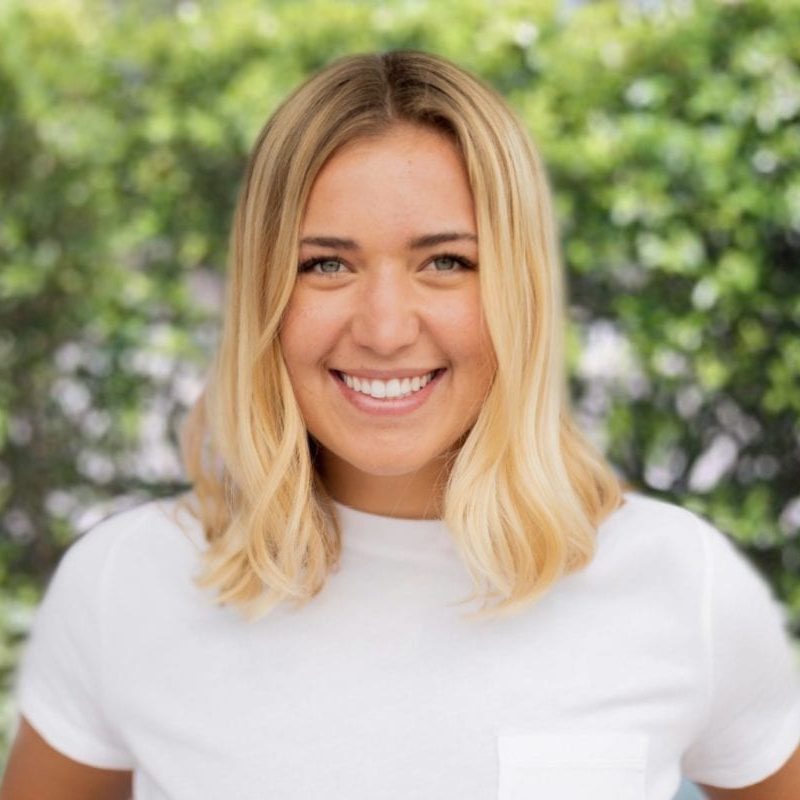
Julia Carlson
Media/REsearch Director
I am a 4th year Mechanical Engineering student from San Carlos, California. Upon graduation, I will be working at a medical device startup in the Bay Area, among other adventures. I am looking forward to continuing to utilize my technical skills to solve real world problems and improve the lives of others. In my free time I love to ski, hike, and paint.
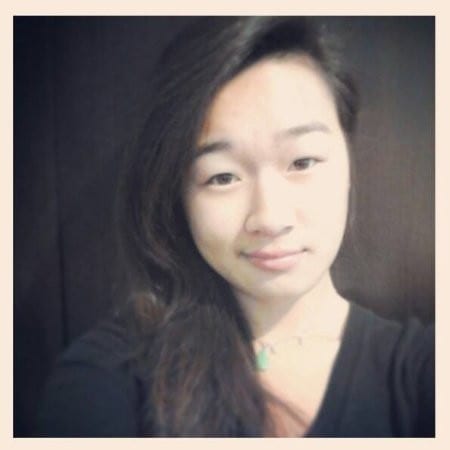
Becky Lu
Editor/Design Engineer
I am a 6th year Mechanical Engineering student from Los Angeles, California. I look forward to pursuing a career in the automotive or manufacturing industry after graduation. I enjoy trying new restaurants, cooking, and playing video games.
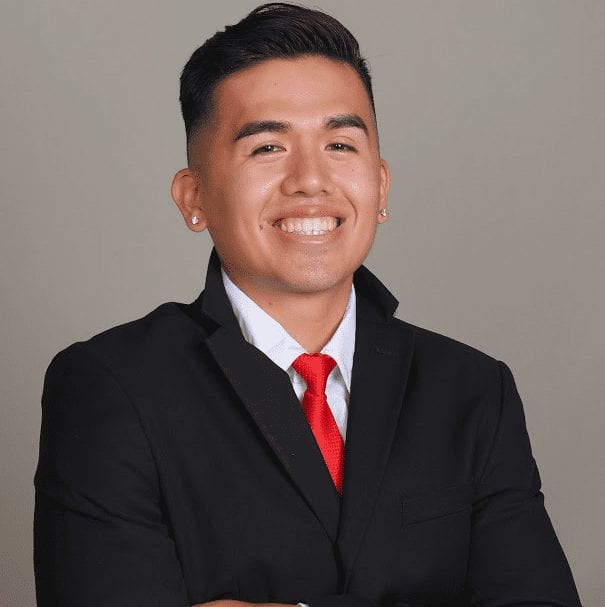
Jomil Aquipel
Manufacturing/
Research Lead
I am a 4th year Mechanical Engineering student from San Diego, California. After graduation, I am starting at a rotational program for Parker Hannifin in their HVAC department as a sales engineer in St Louis, Missouri. I worked on this project to help design an affordable way for people to stay safe from COVID-19.
Acknowledgements
We would like to thank the following individuals: our advisor, Dr. Andrew Kean, for his guidance and valuable input throughout the duration of our project, Dr. Hans Mayer for his consultations and expertise while researching testing methods that would best suit our project, Meredith Rubin for her diligence while purchasing the materials needed for our project, Moncerratt Peralta for helping us design this webpage, and our sponsor, Dr. John Chen, for his good-natured support and funding of our project.
Thank you so much for all that you have done for us. Because of your help and assistance, we were able to succeed.
Our Project's Video
Our Project's Digital Poster
Overview of Problem
Traditional disposable and cloth face masks quickly become uncomfortable during long durations of use. They also inhibit communication, muffling the user’s voice, making it hard for them to be understood, and eliminates the visual communication cues necessary in interacting with others. There are products available on the market that address these concerns.
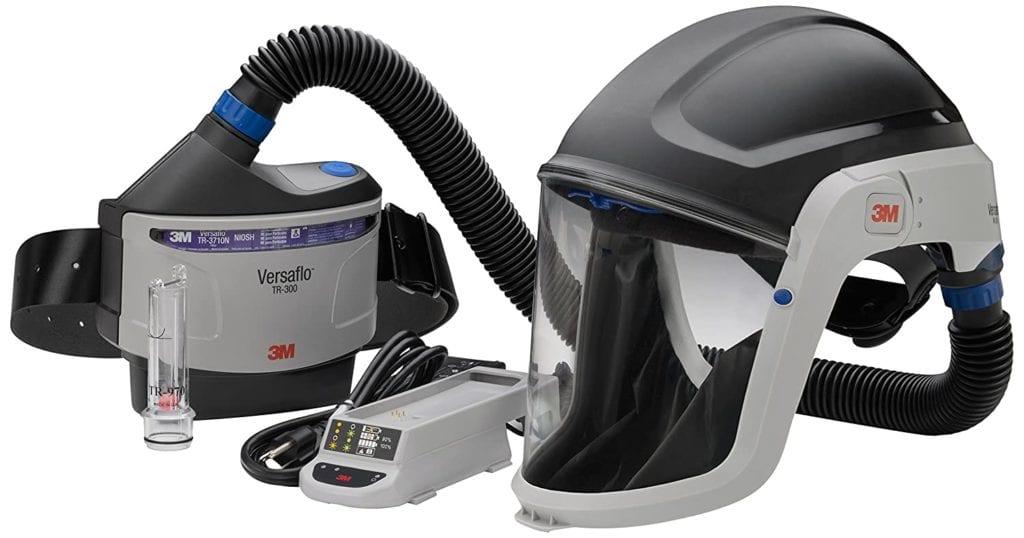
This is a powered air purifying respirator, or PAPR. The starting cost for a PAPR is around $1500.
The purpose of our project was to design a laminar flow face shield with commercially available parts that would not inhibit the user’s visual communication cues.
Our target audience are Cal Poly professors and working individuals who need to wear a mask for long durations of time and who need to communicate effectively while wearing a mask.
Engineering Specifications
The final project design must meet the following criteria:
- Filters 99.90% of particles ≥ 0.3 microns
- 6+ hour battery life
- ≥ 4.06 cfm filtered air flow rate
- verbal and visual communication not significantly impeded
- Cost < $200
- Weighs < 5 lbs
- ≥ 70% appearance approval rating
Engineering Analysis
Positive pressure
For our design, we decided on a closed-faced shield. A closed-faced shield requires a lower flow rate to meet the Center of Disease Control (CDC) guidelines on PAPRs.
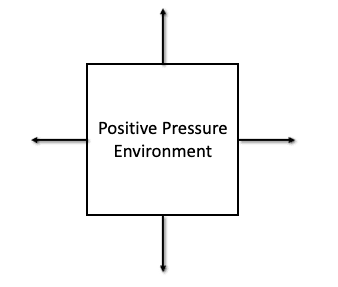
The positive pressure environment inside the mask impedes particles from going inside the shield. Air particles go from high to low pressures in the same way current goes through the route of least resistance. Therefore, we can conclude only the particles should go in through the blower and filter, securing the user from unfiltered air.
No filter on outflow
Our project scope did not require us to filter the outflow air, but we looked into the idea to protect others as well. However, effectively filtering out the air was difficult with the given time frame. First, filters have to be sized and used only at that rated size, meaning sheet filters would be ineffective. Then, there needs to be an outflow of air in the mask and an added filter would block the exits on the mask. At last, testing the efficacy of the filters would be difficult since we would need a control room on the outside of the mask to test this. We can’t create this with a home 3D printer, so we would need more resources. Given these difficulties, we moved forward without filtering the outflow air.
Blower sizing/Losses through blow and hose
When deciding which blower to use in our design, we purchased multiple blowers. We tested the blowers using a flow anemometer to confirm they produced a flowrate greater than 4.06 cfm, the CDC recommended flowrate for a tightly-sealed PAPR. We then chose a blower that had a safety factor four times greater than this recommended flowrate to account for losses through the attachments, hose, and face shield.
CAD Model

Please note that the white shield seen in the figure above is not representative of the mask used in the final design. A larger image can be viewed in the Project Gallery.
An animation of the assembly is shown below.
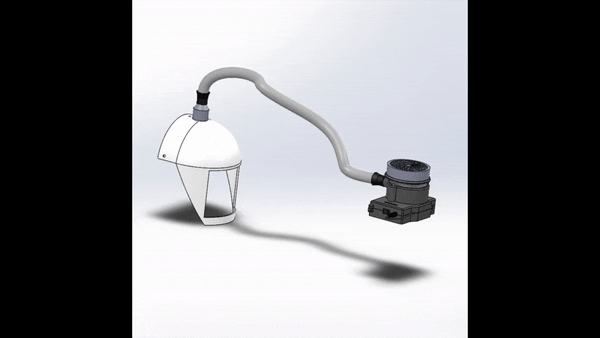
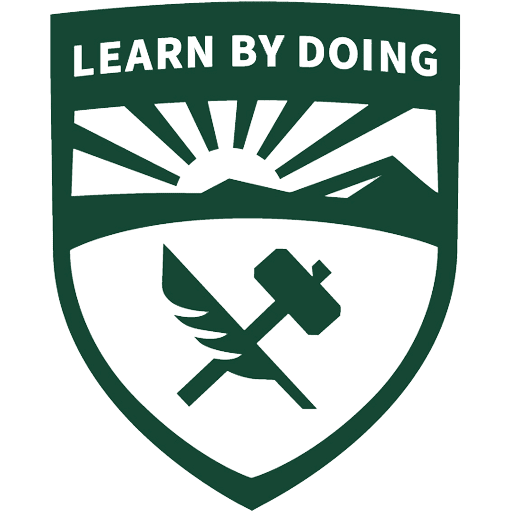
This project is sponsored by Cal Poly Mechanical Engineering professor, Dr. John Chen.
Final Design
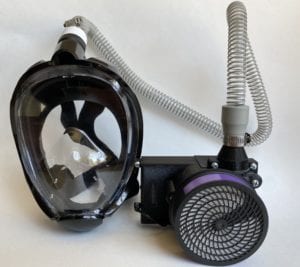
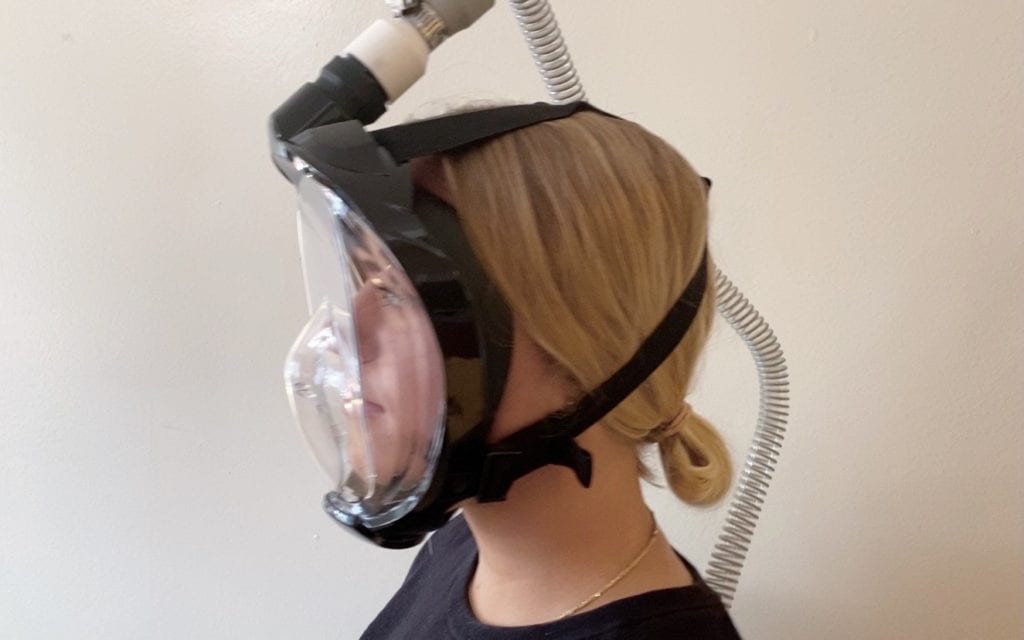
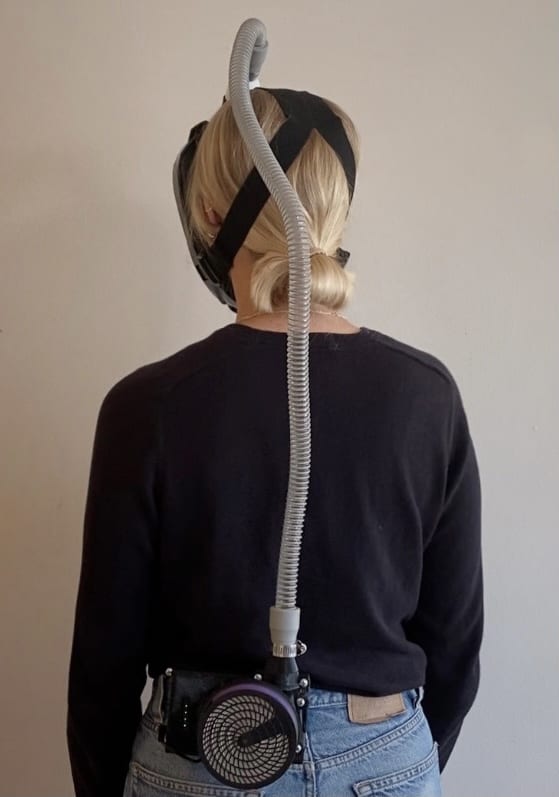
Specifications
Weight (total) -3 lbs
Dimensions (battery pack) -6” X 6” X 5”
We have designed a low-cost, accessible powered air purifying system (PAPR). To provide clean air to the user, the blower sucks air through a threaded cannister HEPA filter, and then pushes it through the hose to the mask. It has a life of ___ hours and has an efficiency of 99.75% that it will filter particles sized 0.3 microns or greater.
Our design attempts to be buildable at home; all of the parts are easily accessed via Amazon or a local hardware store. Assembling the respirator requires more technical savvy, as it requires access to a 3D printer as well as beginner-level soldering skills.
Parts List
- Amazon
- Mask
- Hose
- 12V Blower
- 12V 6000mAh Battery
- HEPA Cannister Filter
- Belt Clips
- 2.1mm DC Male to Open Cable
- XT60 Connector
- Hardware Store
- 2-1/2″ O-ring
- 1-5/8″ O-ring
- #10-24 x 3/8″ Screws (3x)
- #10-24 1/2″ Screws (4x)
- 1-1/4″ Hose Clamps (2x)
3d Printing manufacturing and design
There are three parts which are 3D printed: the hose-mask connector and the top half and bottom half of the housing. Both components were modeled in SolidWorks and imported as stl files to Cura, which provided the g-code to print the parts.
All parts were printed out of PLA, however, our ABS is acceptable as long as it is compatible with the printer in use.
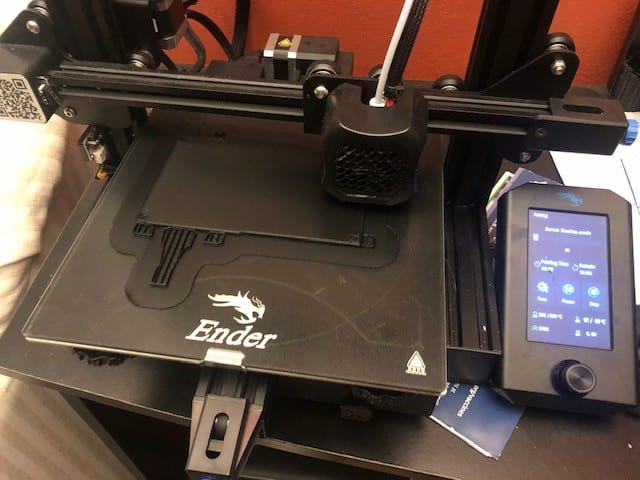
To aid in manufacturing these parts, the stl files have been posted online at thingiverse.com(link below). It is highly recommended that the wall thickness be at least 2 and the infill density be at least 15% to encourage structural strength.
Soldering
The blower and the battery are connected by a 2.1mm DC male to open cable with XT60 connectors soldered to the end of each cable. The solders are protected with a heat shrink.
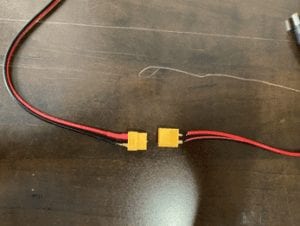
Key Results and Findings
Particle counting
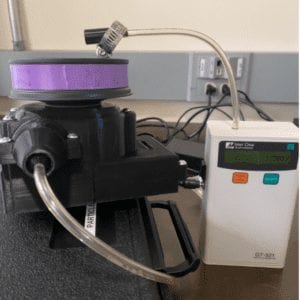
The particle counting test determined the efficacy of our design by calculating our design’s efficiency at obstructing particles sized 0.3 microns or greater from entering the respirator. The test setup to the left was utilized to count the number of particles in the ambient air and the particles at the exit of the blower housing; these readings were then used to determine the efficiency.
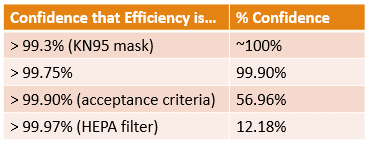
A dataset of 90 different efficiencies was constructed; assuming that the sample set is Gaussian, the confidence intervals above were calculated. Importantly, our design has a 99.90% confidence that it will be 99.75% effective, and nearly 57% confident that it will meet the acceptance criteria efficiency of 99.90% efficient.
flowrate verification
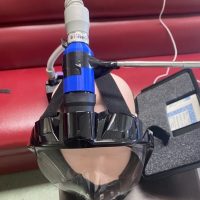
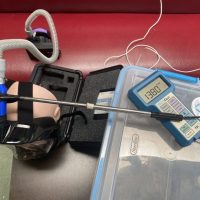
Test set up to verify the flow rate of the filtered air to the user. We 3D printed a custom test duct that fit between the hose outlet and the mask inlet, in which we placed a hot wire anemometer to measure the velocity of the air. This was multiplied by the cross sectional area of the test duct to obtain the volumetric flow rate. We found over a one-hour testing time period our average flow rate to be 11.99 cfm and never dropped below 11.52 cfm. This met and exceeded our acceptance criteria of 4.06 cfm.
User experience
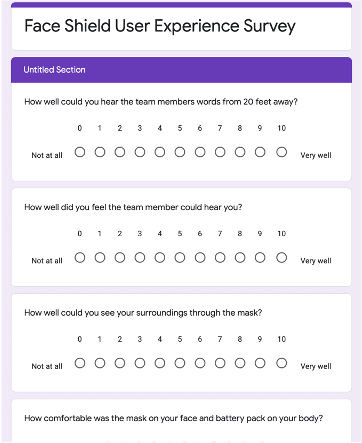
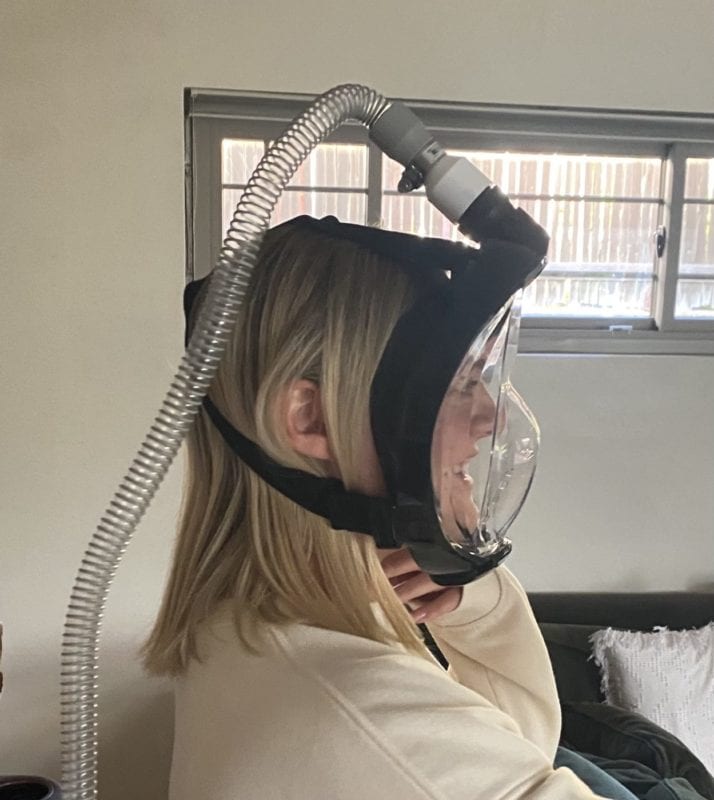
We conducted our experience survey to obtain data on the overall comfort, visibility, communication ability, and aesthetic appeal of our respirator. A volunteer user put on our completed respirator and stood 20 feet away from the team member. Each volunteer was given the user experience survey, via Google form, to fill out as the test was run in which they ranked on a 0-10 scale their experience on different criterion. We found communication and comfort scored well and no user’s experience fogging while the mask was running, however, visibility and aesthetic appeal both did not meet our acceptance criteria.
Final specification results
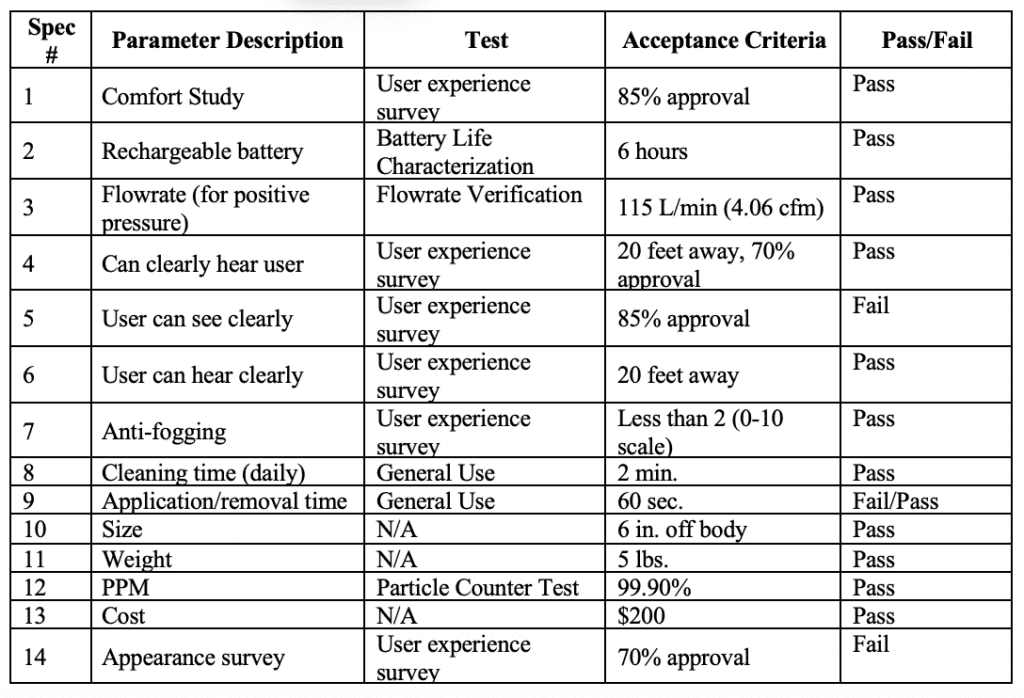
Conclusion and Recommendations
Recommendations:
- Design a test to better analyze communication. Right now our testing only found the volume of a speaker from inside of the mask but the main problem is the clarity of the person. Find an alternative face mask to solve our 2 failed tests. Our respirator performed poorly on aesthetics and visibility from the face mask, and these two could be solved with a sleeker mask. Design a test to find any leakage in our face mask. Although from a physics perspective it is impossible for air to come into a positive pressure, it would not hurt to test this to prove it to be true.
Conclusive Remarks:
- Our respirator performed extremely well on its main function, filtering out viral particles. Considering the pricing is 10 times lower than the average respirator on the market, overall our project was a success.