Our Team
We are the Cisco 1RU Standardization team. All of our team members are mechanical engineering majors at Cal Poly SLO and plan to graduate either this Spring or next Fall. For three quarters, we virtually worked together with Cisco to complete our senior design project. Every member worked from a different location in California and despite the limitations of COVID, our team was still able to bond with one another and complete our deliverables.
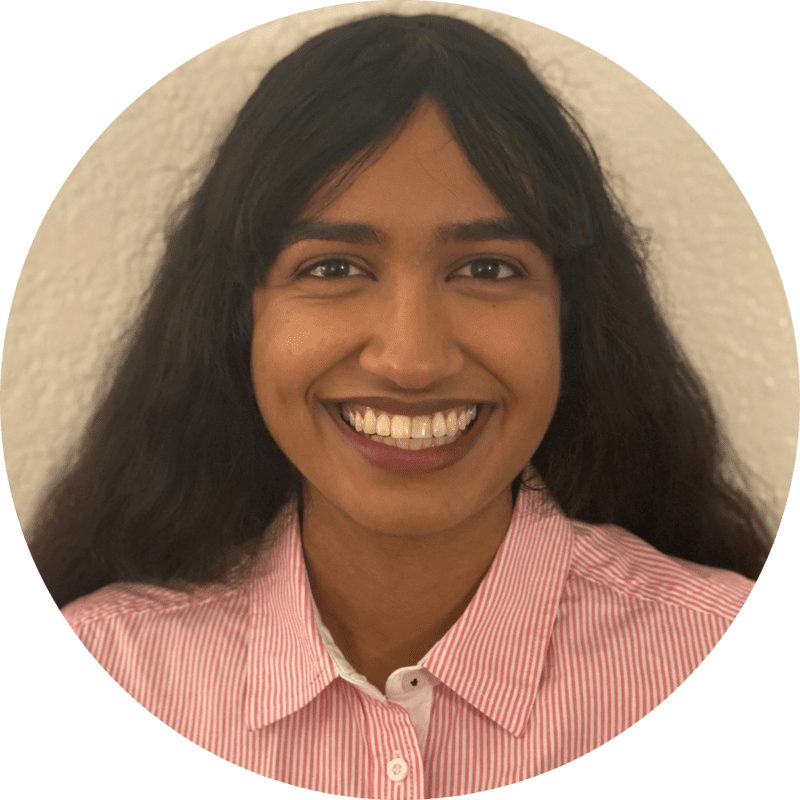
Sarika Singhal
I’m a 4th year General concentration Mechanical Engineer. Before joining the workforce, I plan to pursue a Master’s Degree in Mechanical Engineering. I want to work in quality engineering because it combines my interests in design and manufacturing. Outside of school, I love to paint and watch Netflix.
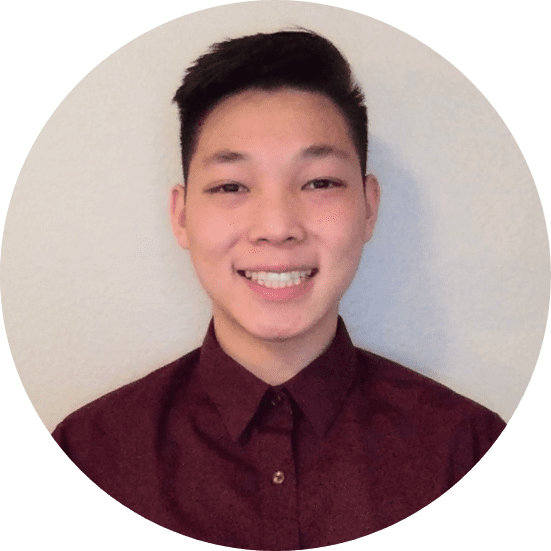
John Liu
I am a 4th year Mechanical Engineering major (general concentration) with a planned graduation date of Fall 2021. I plan to pursue a mechanical/manufacturing design position after graduation. I enjoy traveling, eating good food and exercising in my free time.
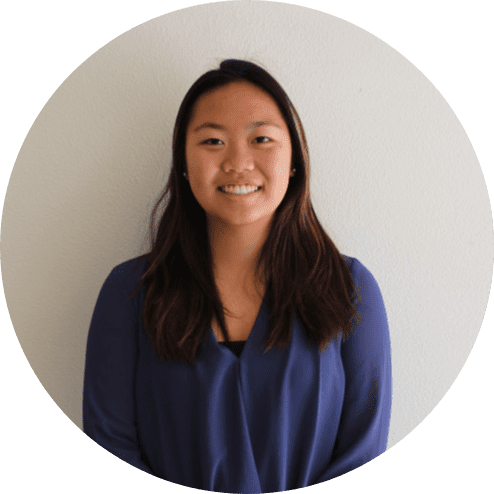
Leia Tashiro
I am a 5th year general concentration Mechanical Engineering major from Honolulu, HI. I will be graduating this Spring and working at Apple as a mechanical design engineer in the Fall. My hobbies include backpacking, surfing, and playing volleyball.
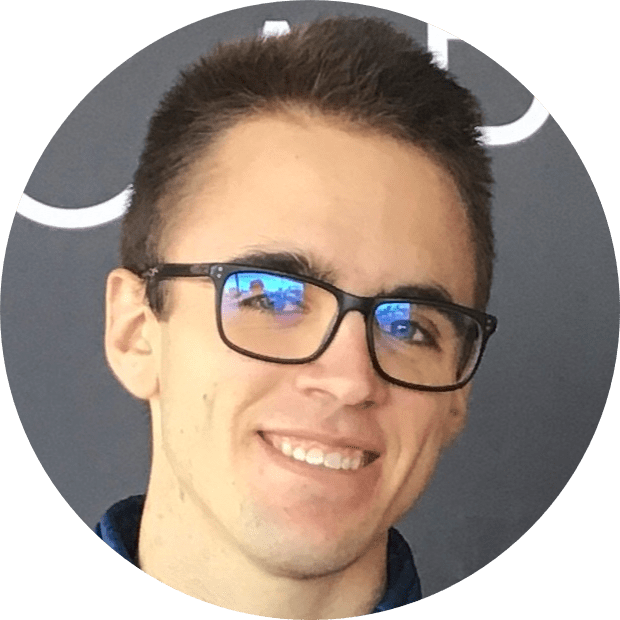
Bryce McNeil
I am a 4th year Mechanical Engineering major concentrating in manufacturing. I am graduating this Spring and am hoping to work in the Bay Area with either design or manufacturing. Outside of school, I enjoy cycling, playing video games, and playing soccer.
Acknowledgements
Thank you to Professor Schuster for guiding us through the design process as well as encouraging us every step of the way for our project.
Thank you to Cisco for giving us the opportunity to work with a larger company and providing us the necessary resources to improve and iterate our project.
Our Project's Videos
Instructional Video does not include audio. Please follow along with the Instructional Documents.
Our Project's Digital Poster
Background
Cisco’s many different server and router types are currently accommodated with a unique chassis for each type. This affects costs for hard tooling since each chassis consequently has its own tooling. By focusing on mounting hole locations, we can simplify the tooling and leverage existing ones for future chassis. The Cisco team came to us with this issue and requested a documented standardization guideline and a tool to help them design future chassis.
Problem Statement
Our sponsor has asked our team to come up with a way to design a chassis that will serve multiple PCBs with an emphasis on the mounting locations.
Design Process
1. We received 24 CAD files of chassis from different families. All coordinates for mounting hole locations were logged in an excel file and plotted.
2. We then created A MATLAB script to find high density hole locations.
3. After analyzing and presenting our scattered results (as shown below) to the Cisco team our sponsors decided to give us a new set of CAD files from a single family (Quake Family).
4. Our team repeated the process of logging hole coordinates for the new Quake family files.
5. We discussed an alternative approach for our MATLAB tool that would help determine mounting hole locations for future chassis designs.
6. Standardization documents were also created to serve as a guide for future standardization projects.
7. Four rounds of iterations were executed to refine our tool and standardization documents. Each round included procedures, documents, and a MATLAB tool along with a feedback survey.
Design Change
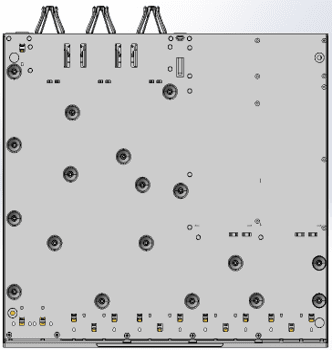
The initial design direction had us analyzing 24 chassis from different families. This resulted in low opportunity for standardization.
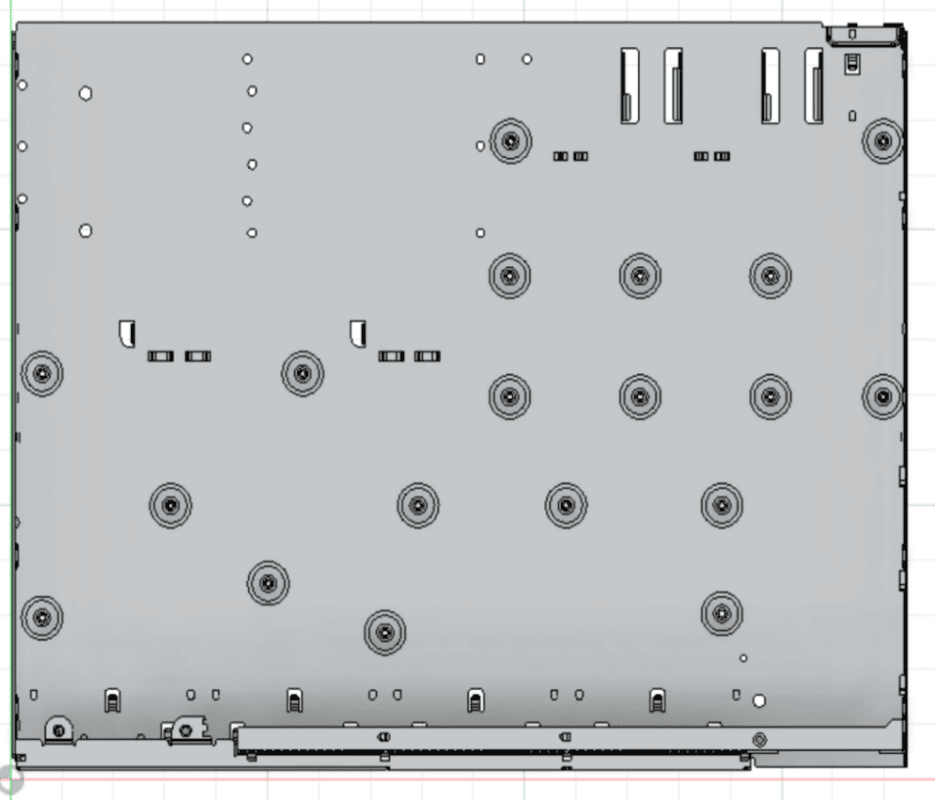
Our new design direction focused solely on the Quake chassis family. This consisted of 18 chassis with a high number of similarities.
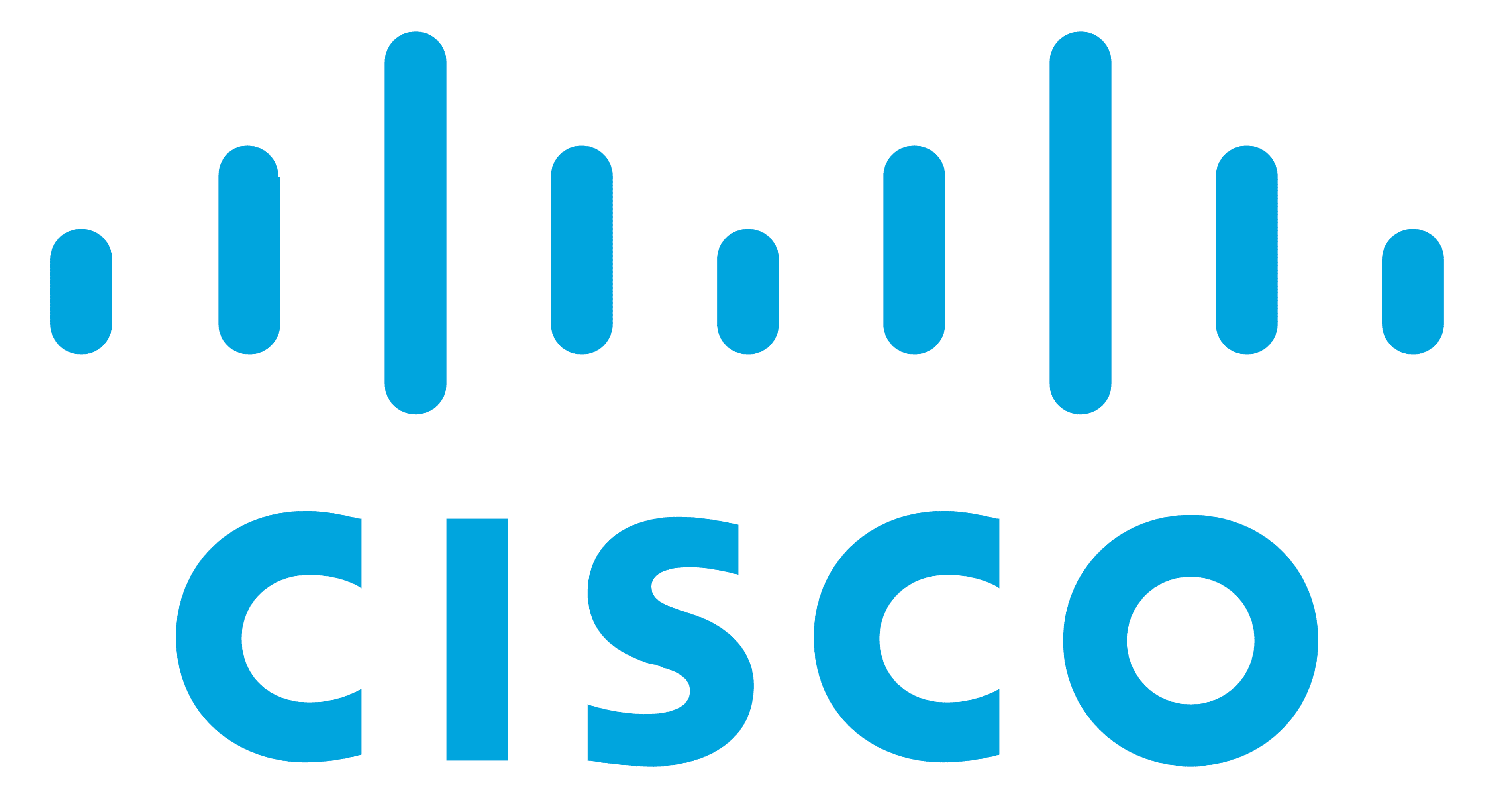
This project is sponsored by...
Hole Locations
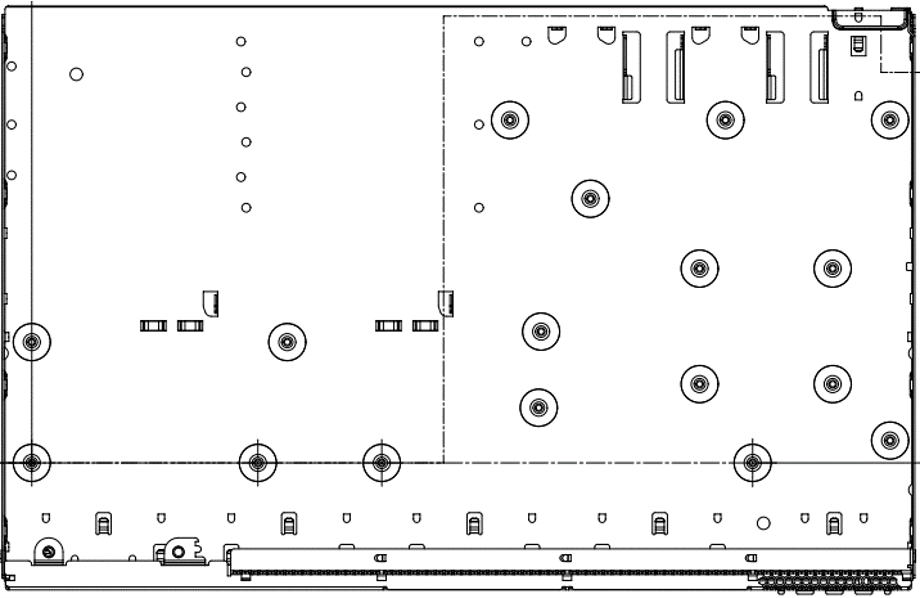
Quake Hole Analysis
Our analysis began by plotting each point into an Excel spreadsheet that could be easily analyzed. We used SolidWorks to measure each coordinate in which the origin was always the bottom left hole for the Quake chassis. This allowed us to easily compare all chassis. After recording all data, 8 of the chassis had a depth of 11.2″ and 10 had a depth of 13.6″. This data was then used to develop the MATLAB tool and propose standardized locations.
Below is an example of our data collection in Excel.
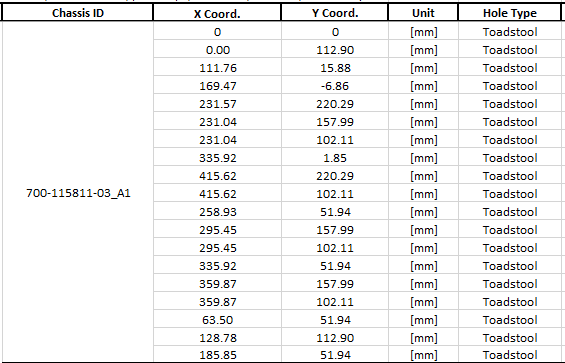
Our Sponsors
Greg Twiss
Peter Wu
Christine Nolan-Brady
Design Verification
Prototype Iteration
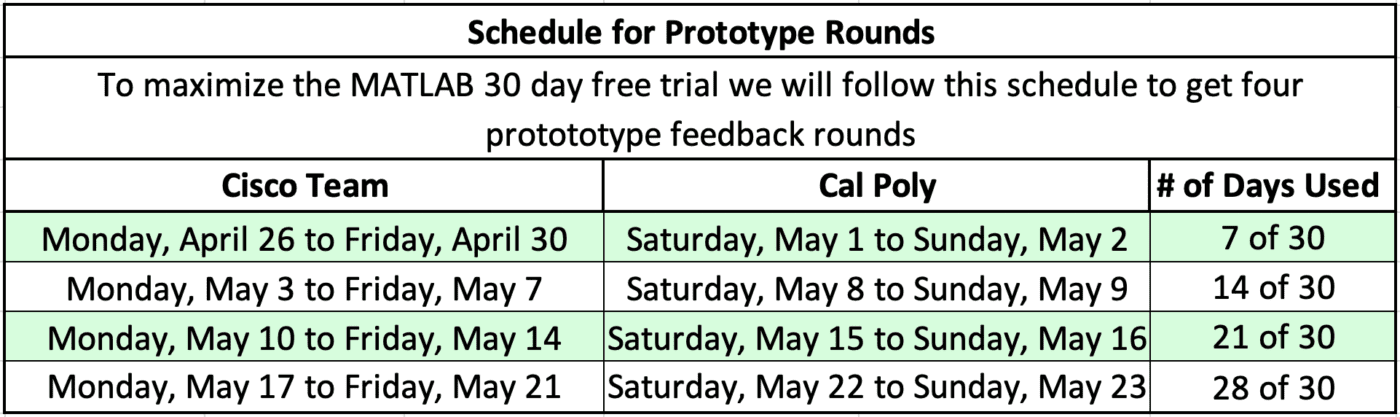
To ensure our documents and MATLAB code met Cisco’s expectations, we had four prototype iteration rounds. The weekdays were dedicated to Cisco engineers and the weekends were dedicated for us to make the necessary changes. During each prototype round the Cisco engineers were tasked with reviewing the material sent to them and providing feedback via a Google Form. The Google Form survey can be found here. We tested the standardization document for user friendliness and ease of application to new Cisco chassis. We tested the MATLAB code for repeatability and made sure it was intuitive to the user.
MATLAB Tool
Goal: To rank the selected chassis by how well it matches the tooling
Why: To help Cisco make standardization cases for their current tooling
How it works: The code runs through each chassis set hole location with a selected set of tooling location and counts every time a pair of holes are within a certain distance from another. As an output, it ranks based on count number per chassis set. (Ex. design1 = 16 means 16 holes of that chassis are within the input distance from the set of tooling location.)
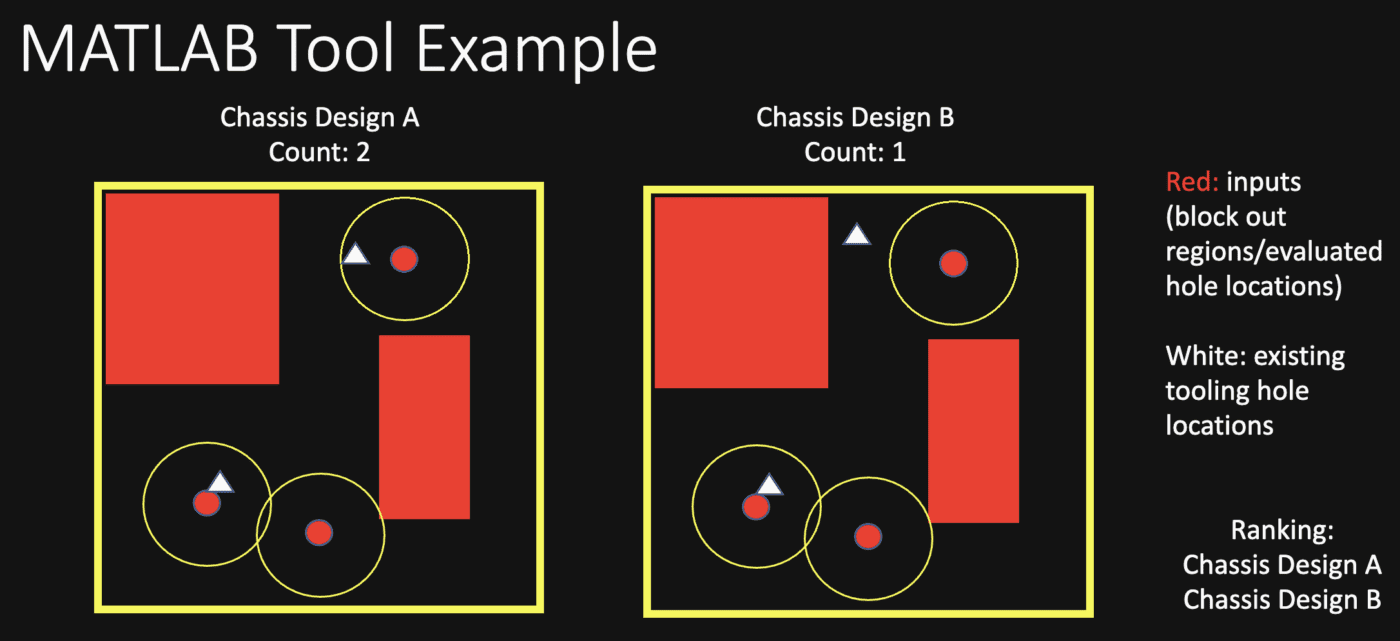
Hole Standardization
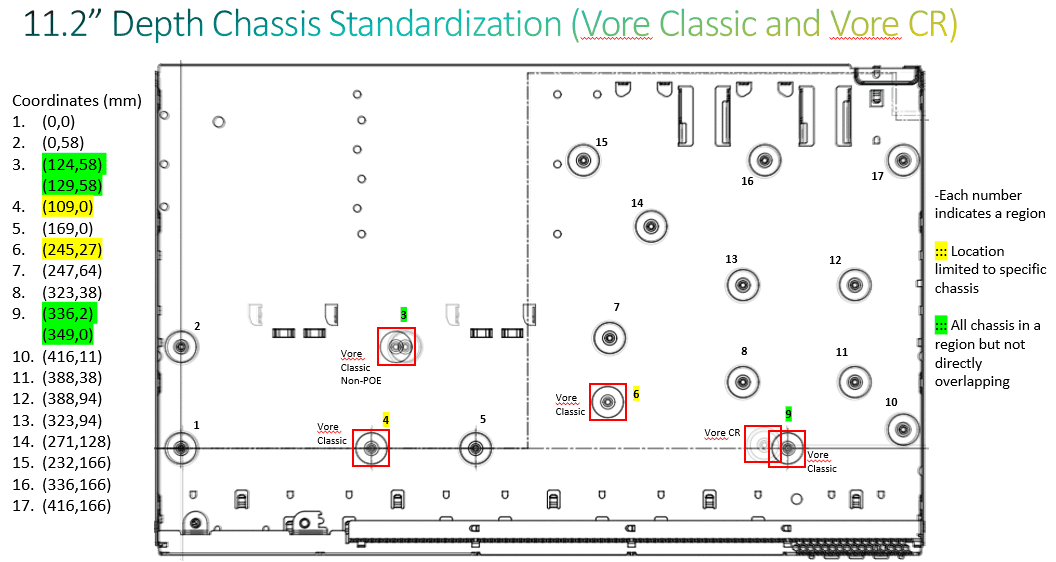
We overlayed each of our 11.2″ and 13.6″ depth chassis to best gauge hole locations. Measured hole locations are recorded on the left, a legend is defined on the right, and the red boxes indicate high capability for standardization. A larger image can be found below for both the 11.2″ and 13.6″ depth Quake chassis.
Project Management
Every week we met with Cisco to discuss our progress. Once a month we met with a variety of Cisco engineers to ask questions and provide an update. Sarika & Bryce focused on the standardization documents. Leia and John focused on the MATLAB code.
Conclusion
In Summary:
- -We completed standardization documents for Quake chassis
- -We created a useful MATLAB tool to promote new designs and build off old designs
-Cisco engineers can design new chassis that utilize existing manufacturing tools
Next Steps:
- -Develop a code that works with CAD alongside MATLAB
- -Iterate on MATLAB code and documentation to better suit Cisco’s needs
- -Automate a hole locator via software
Official Standardization Document
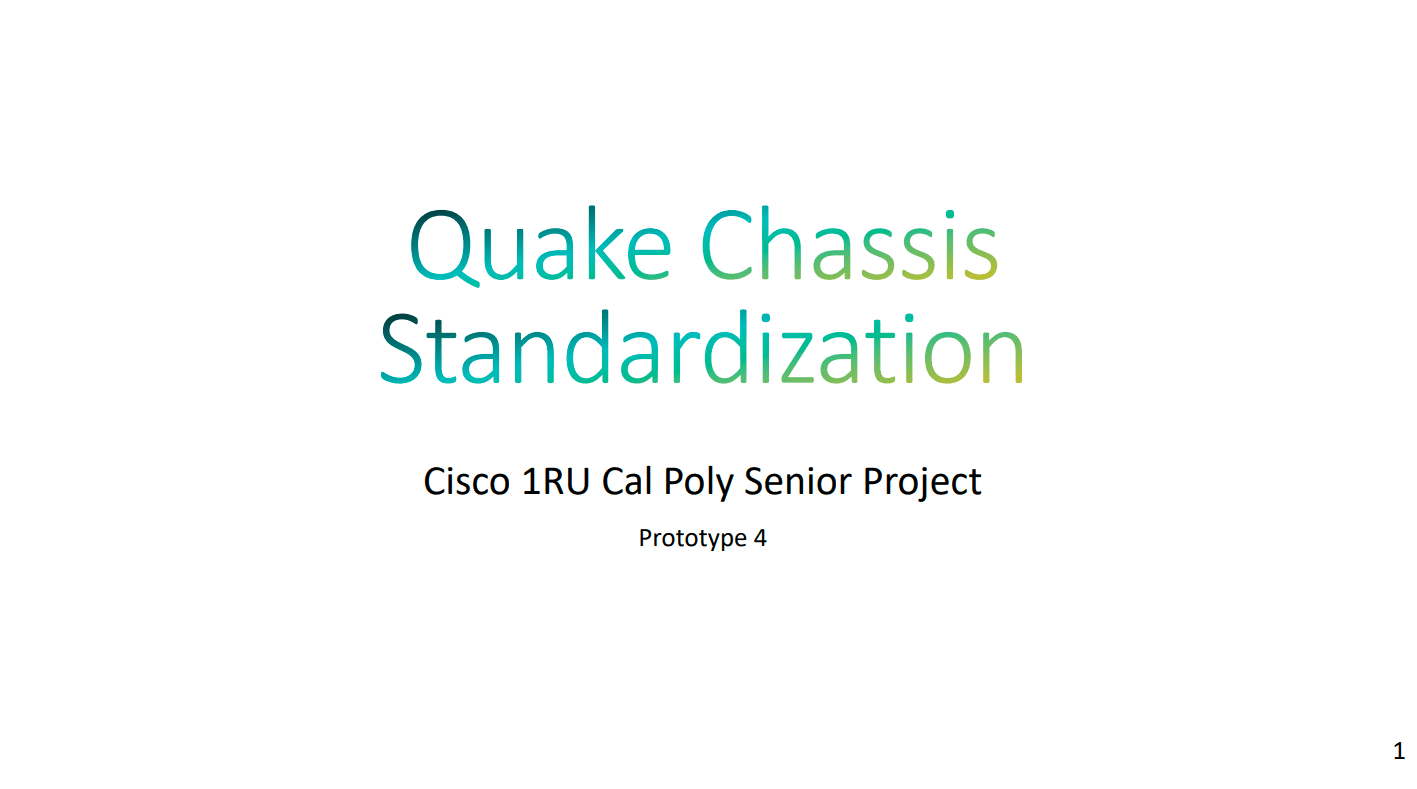
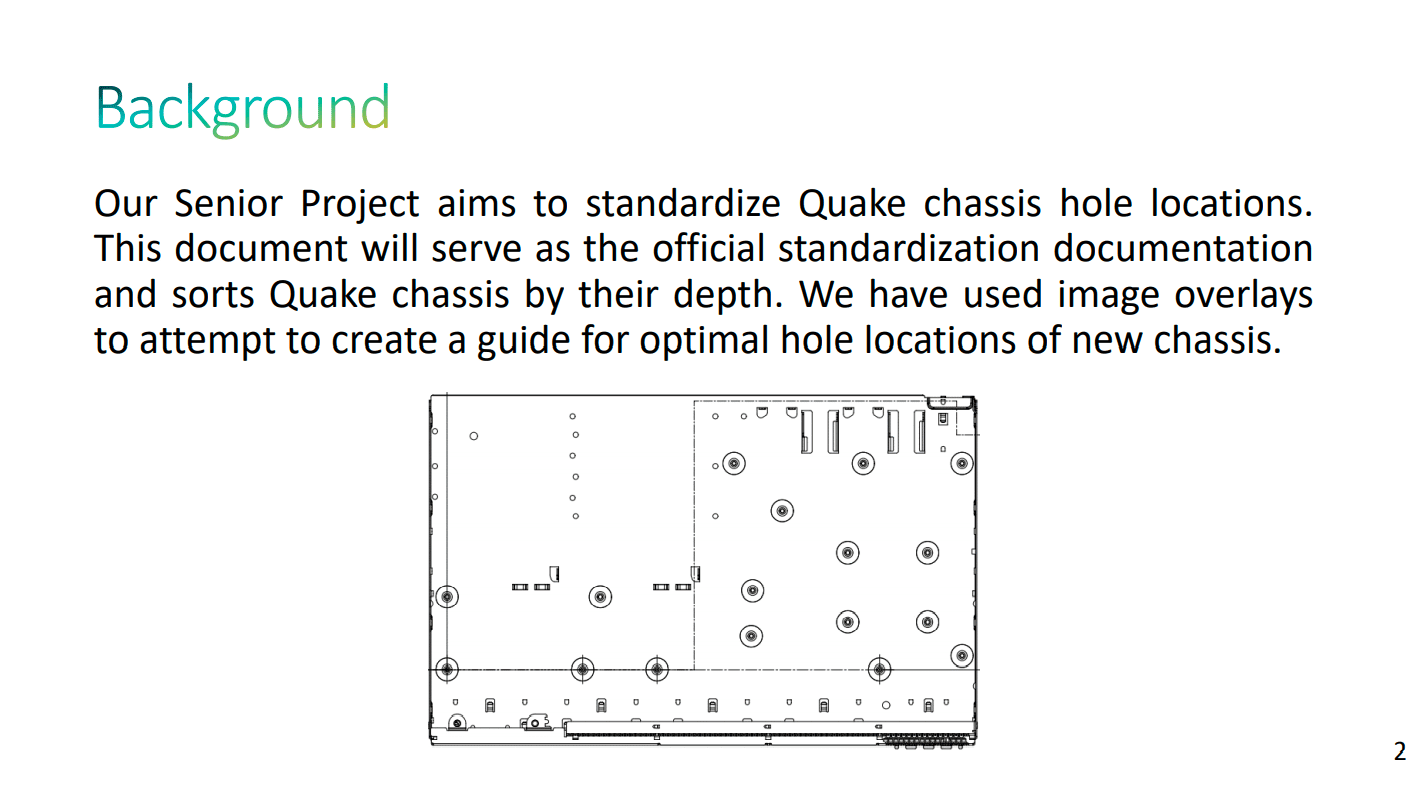
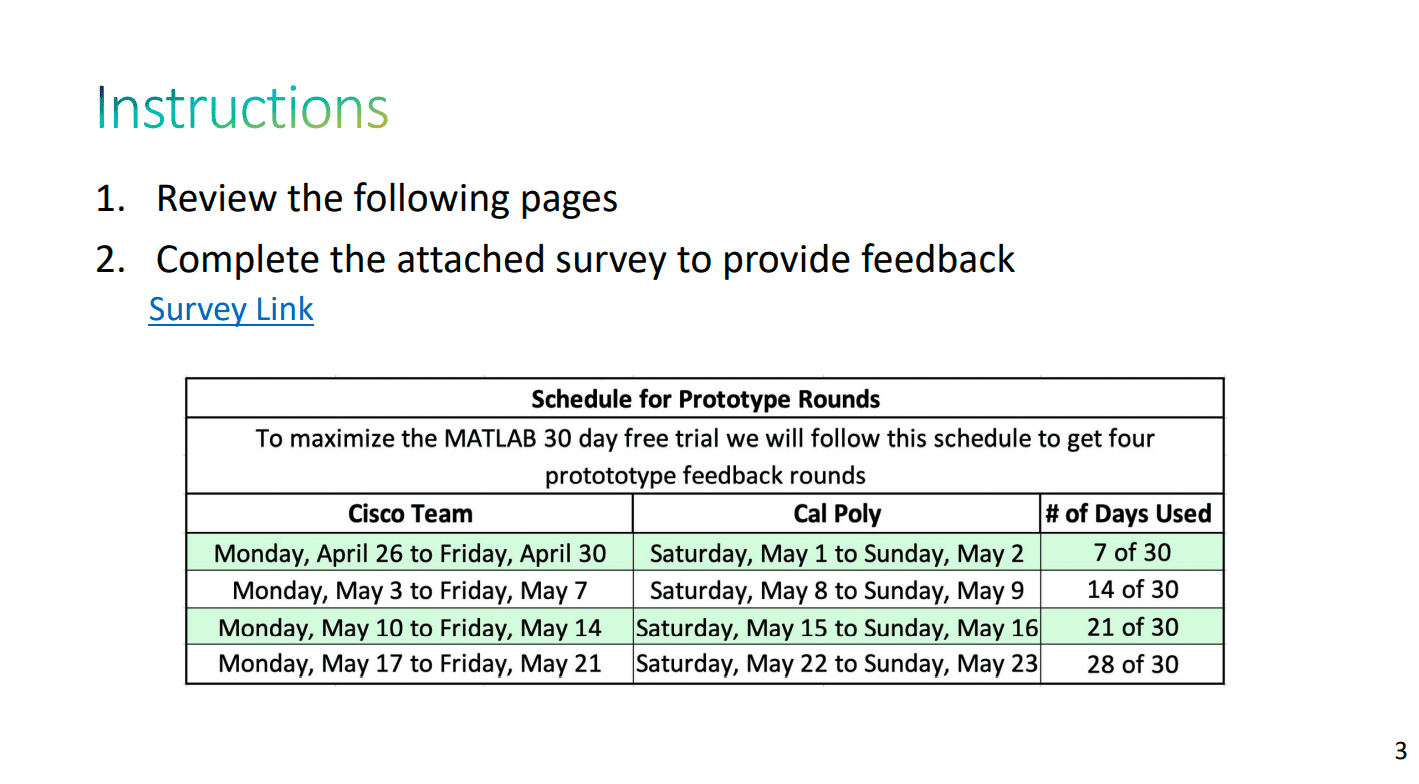
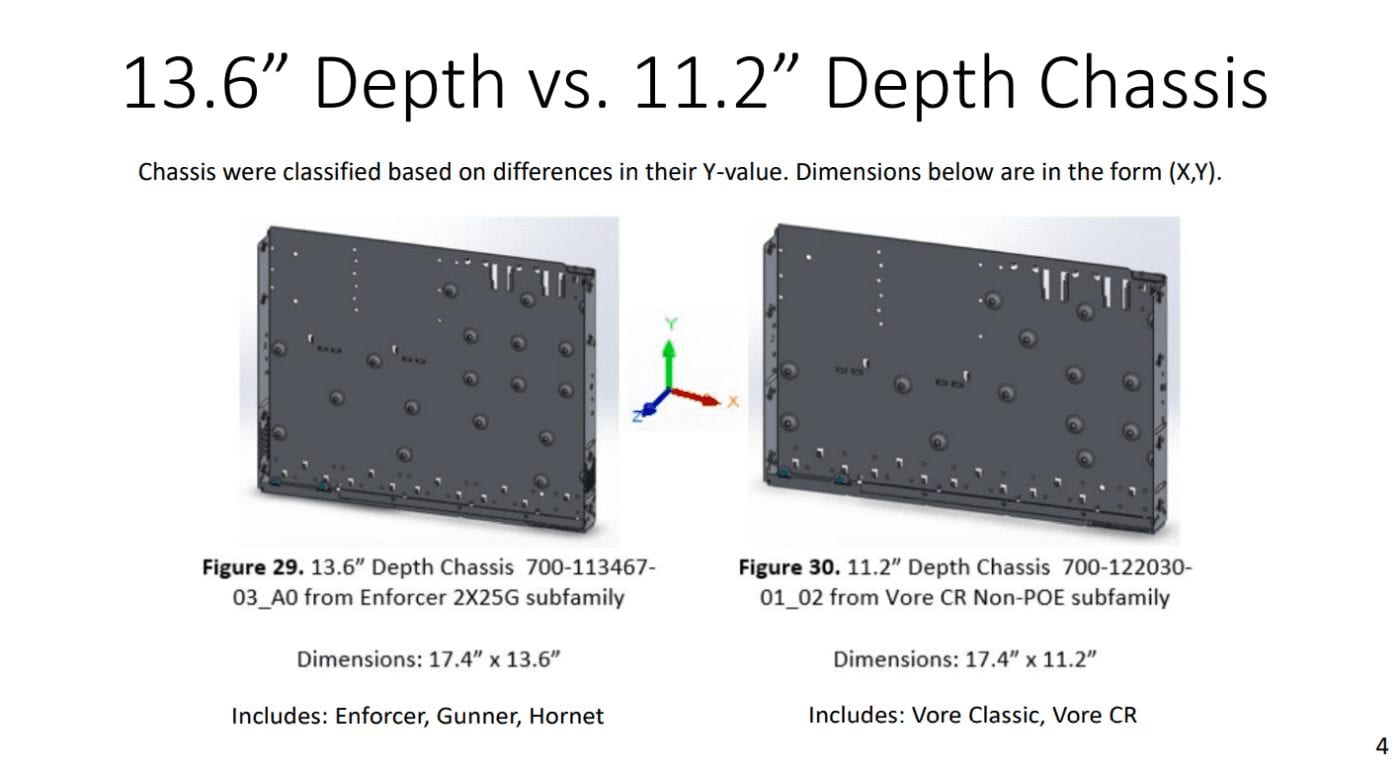
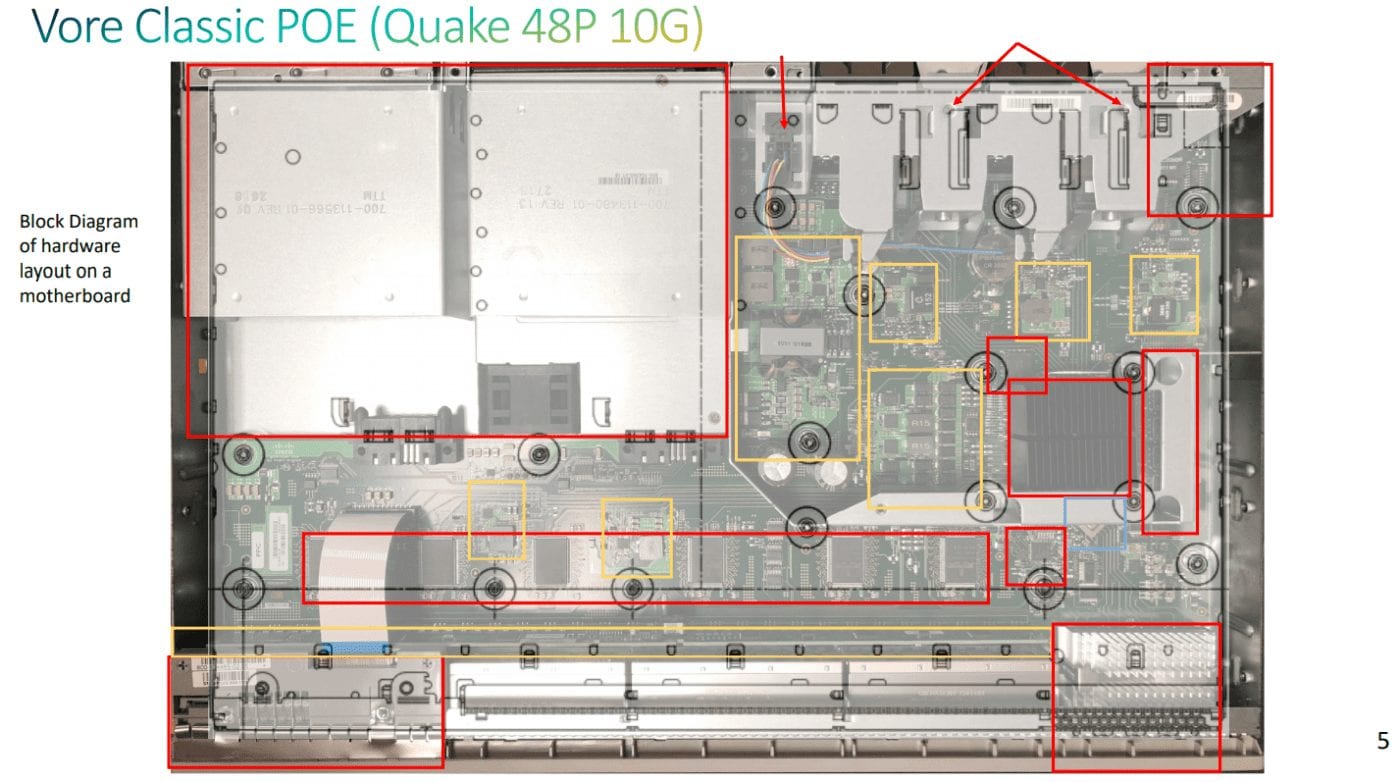
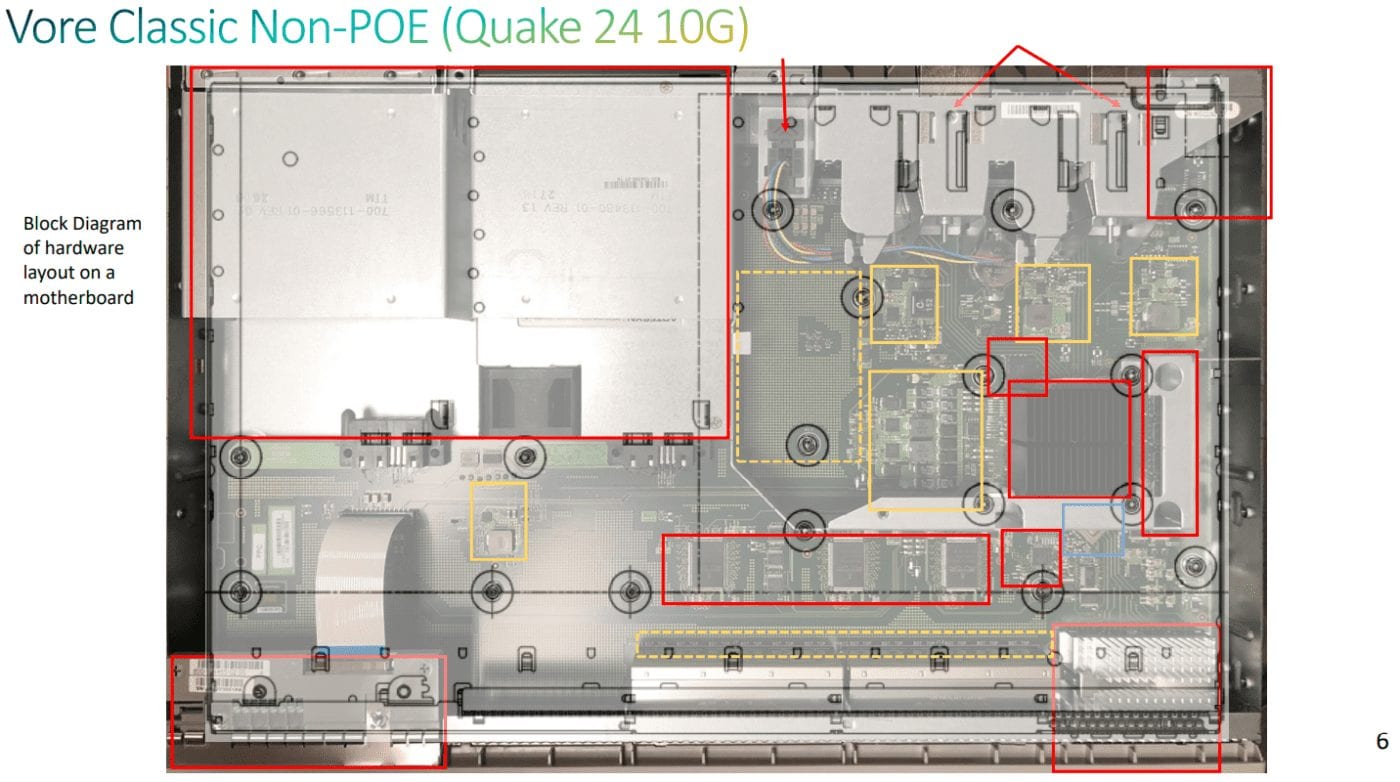
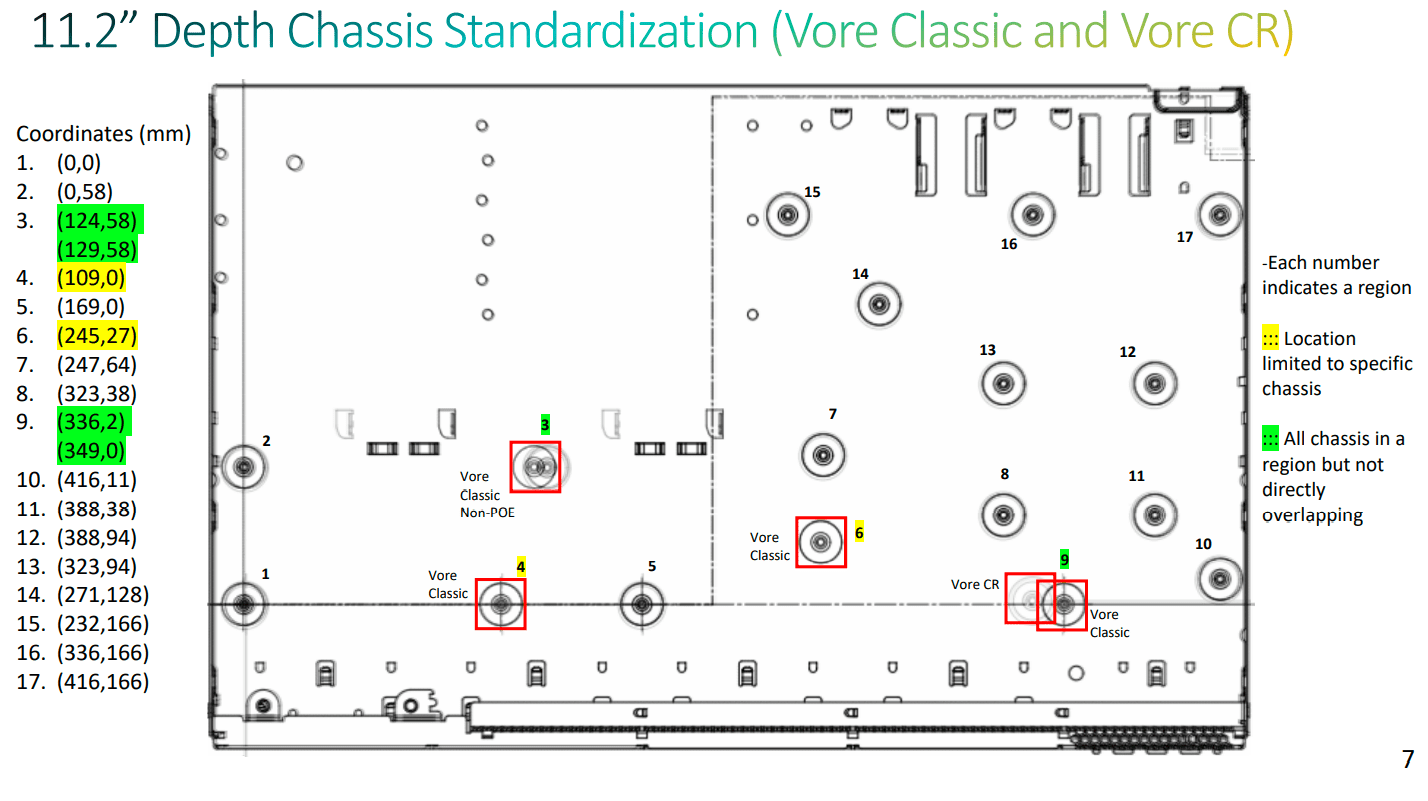
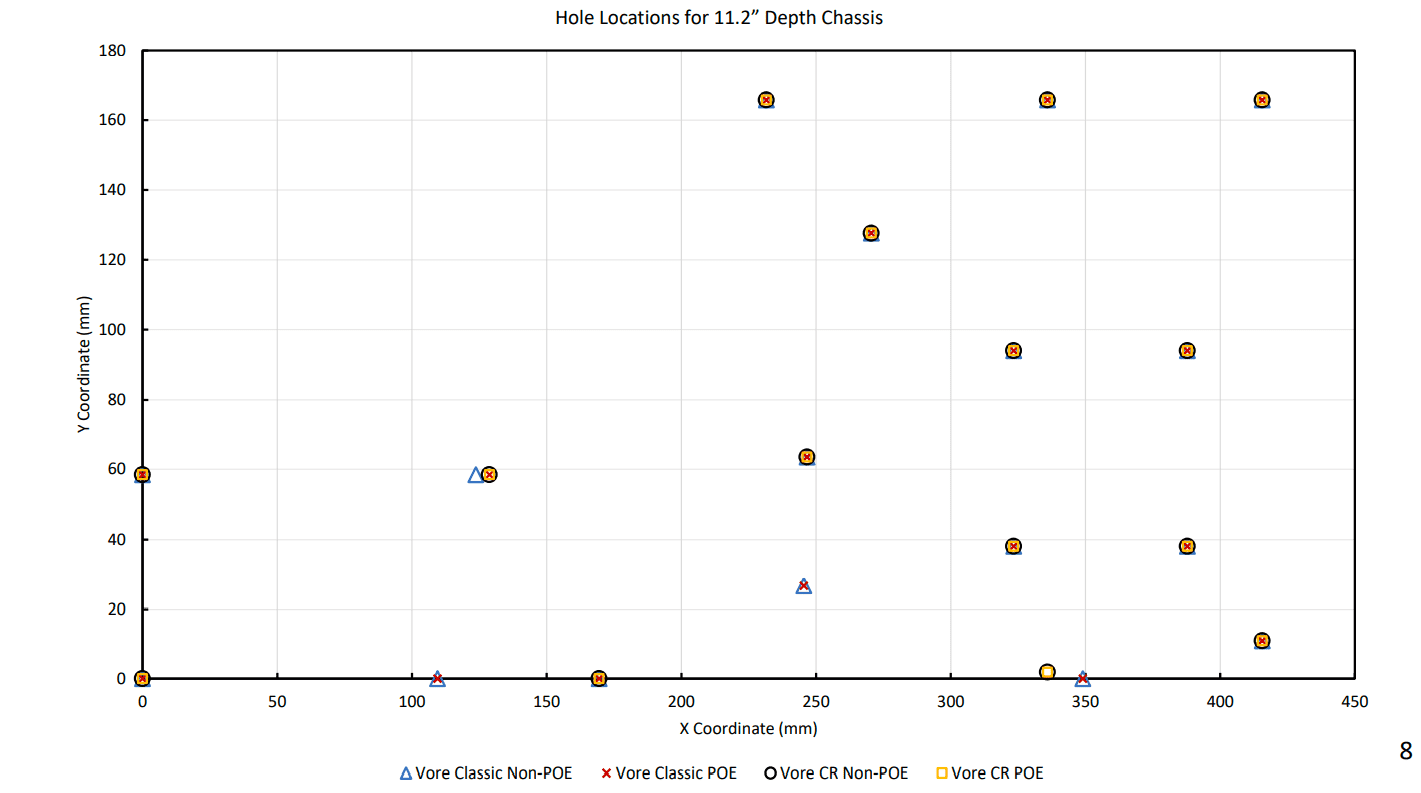
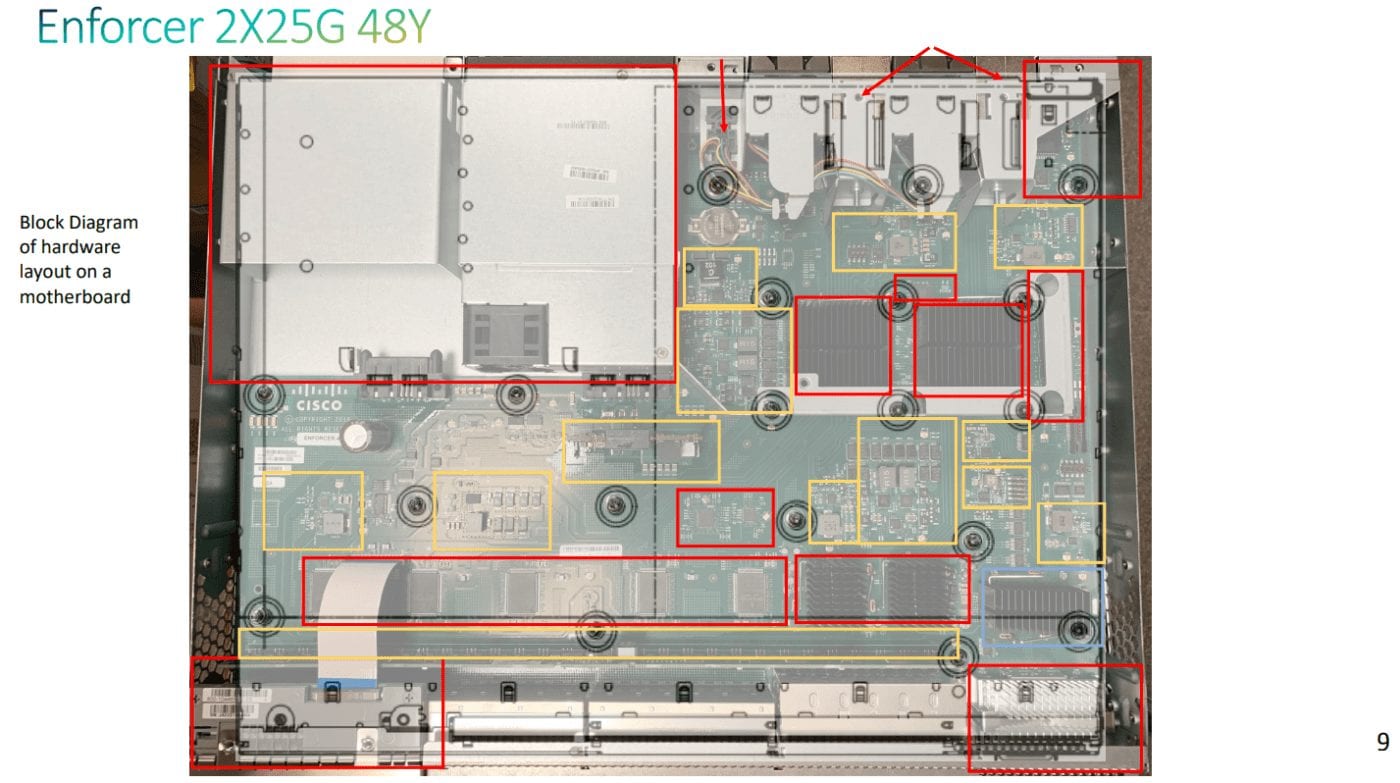
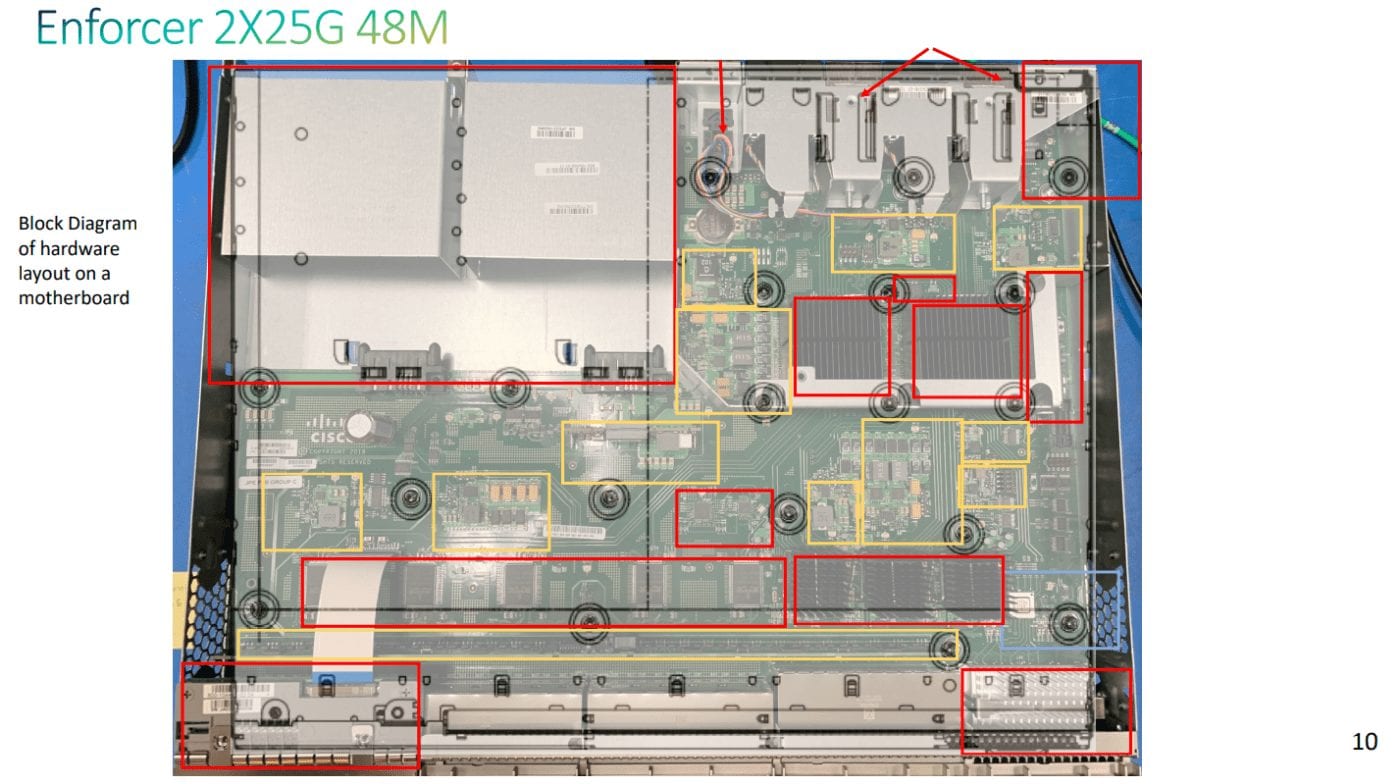
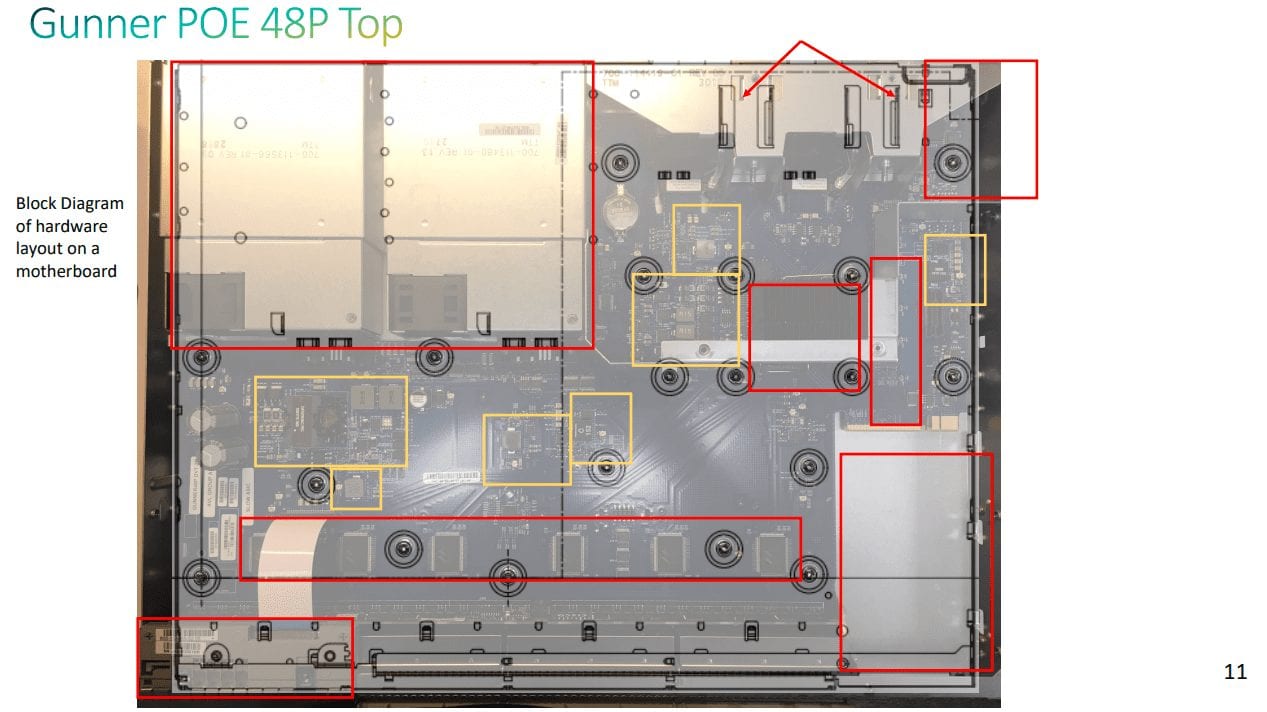
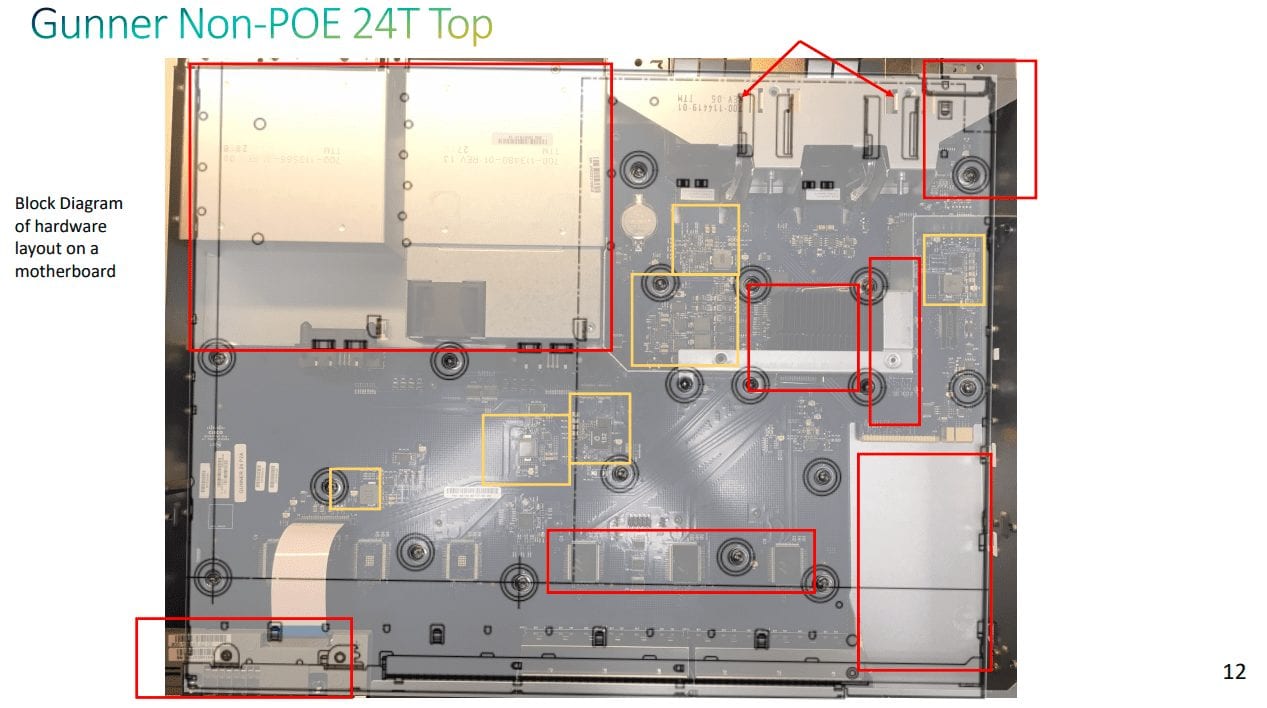
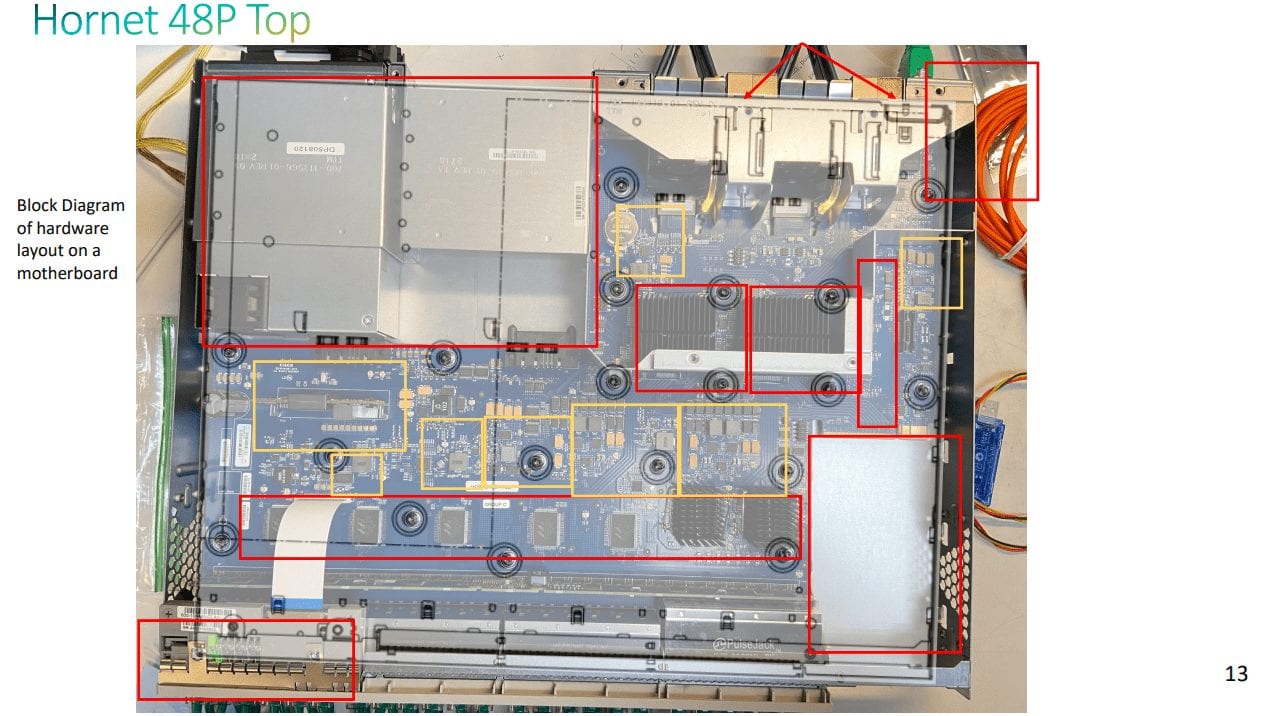
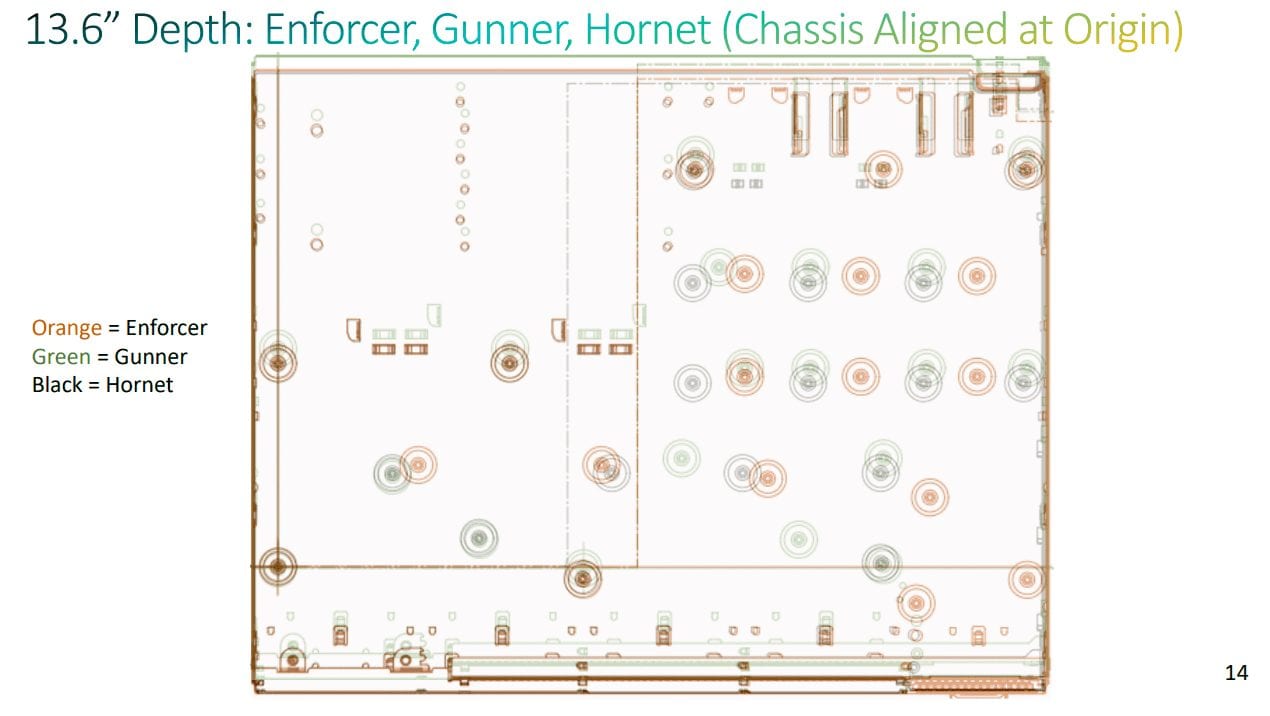
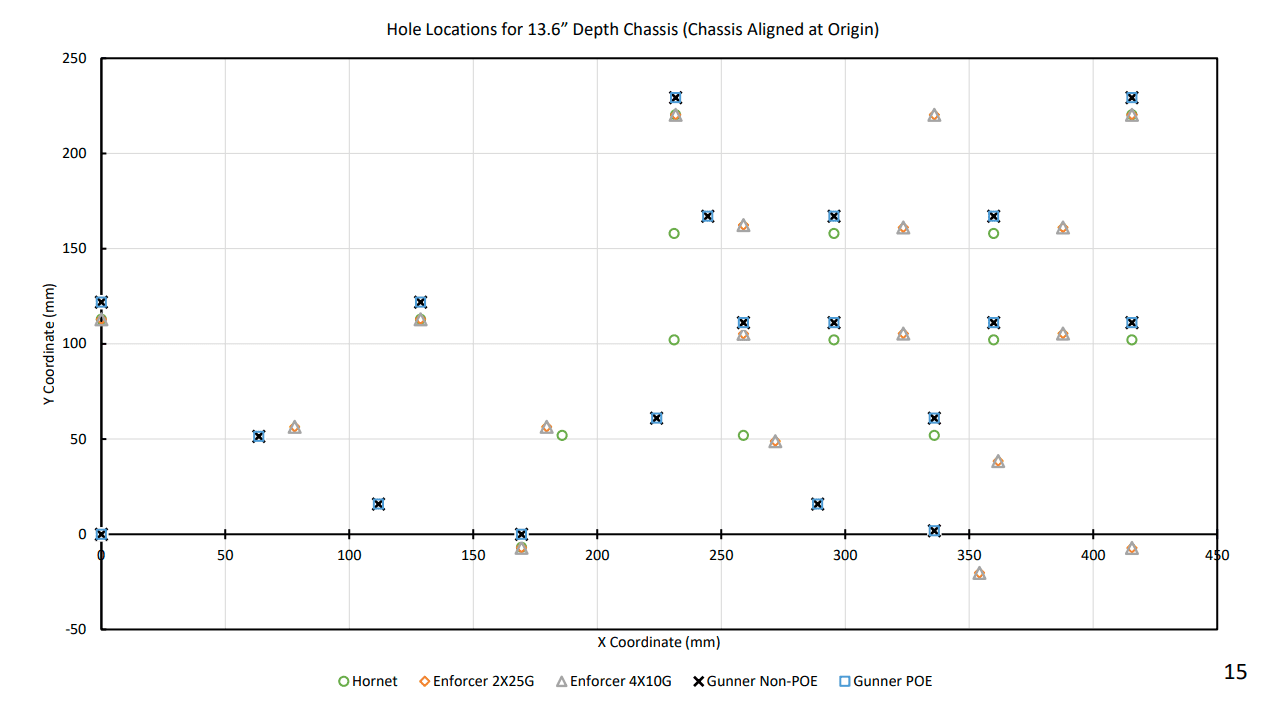
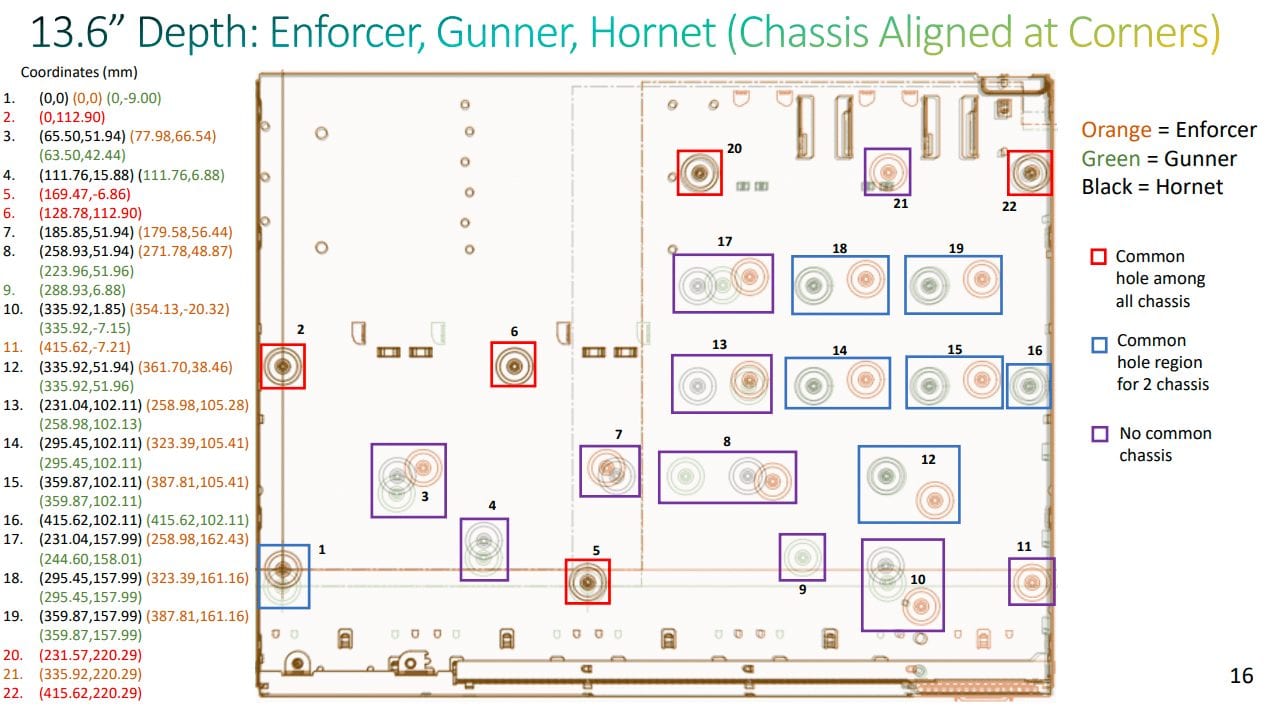
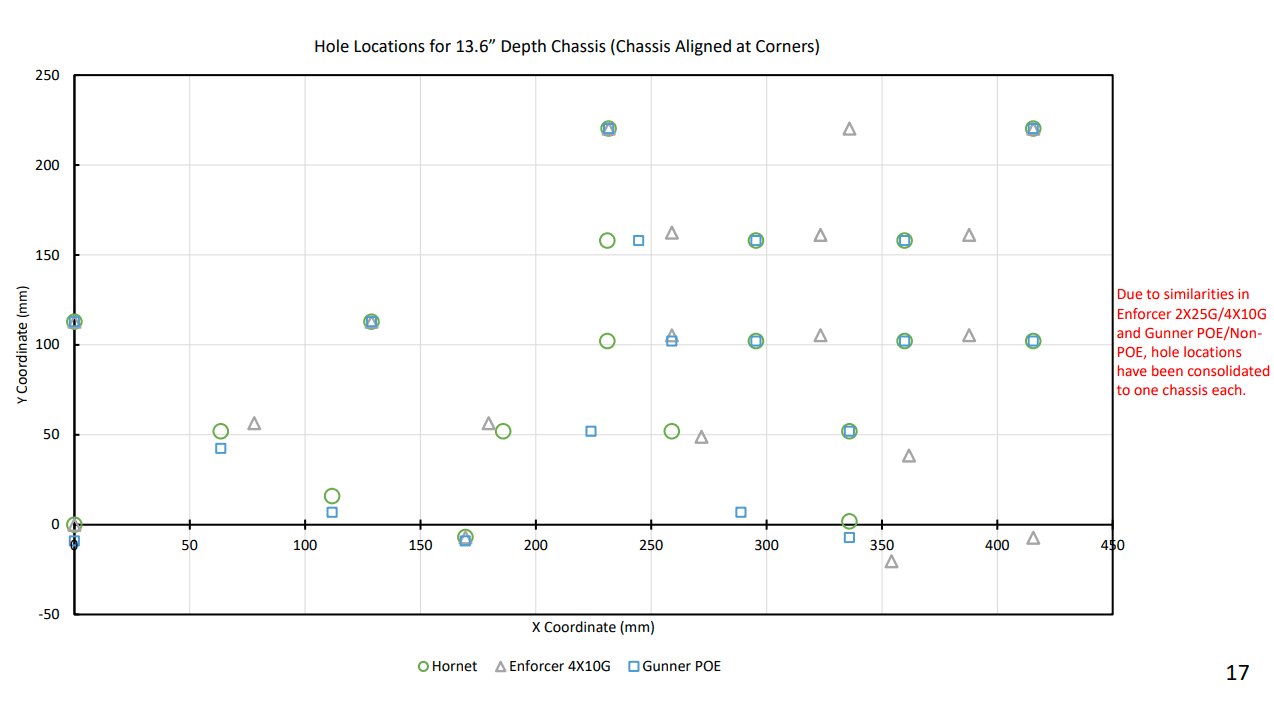
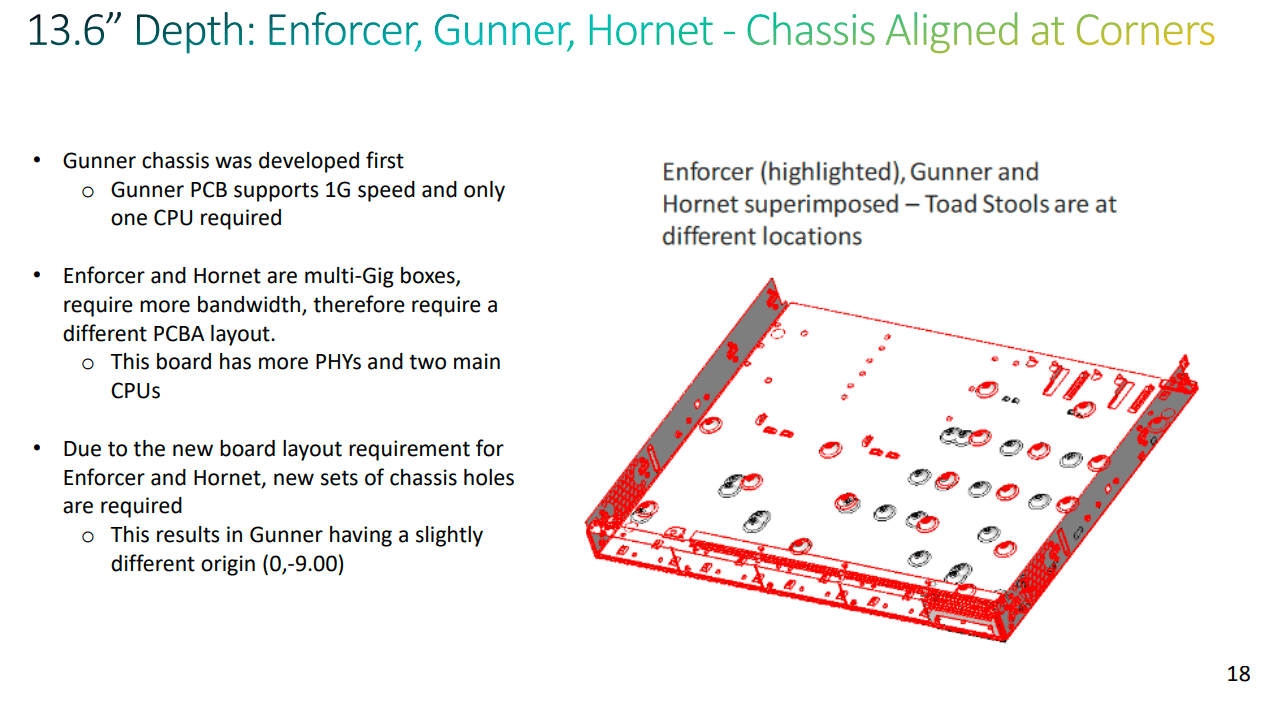