Our Team
Our team, called “Mustangs on the Moon,” consists of three mechanical engineering seniors responsible for the design, build and test of the Sample Container Dispensing Device.
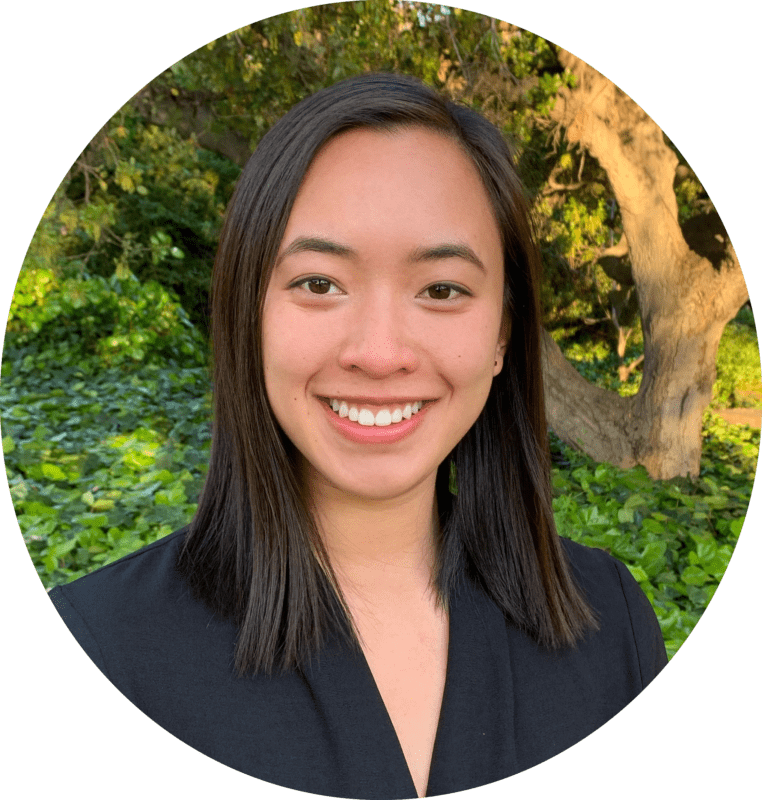
Kristin Kraybill-Voth
Team Lead
Throughout the project, Kristin focused on project management and supported design and build activities. Originally from Denver, CO, Kristin participated in the Prototype Vehicles (PROVE) lab, serving as the project manager for the Solar Car project.
Kristin has accepted a position at Northrop Grumman in Azusa, CA as a mechanical engineer.
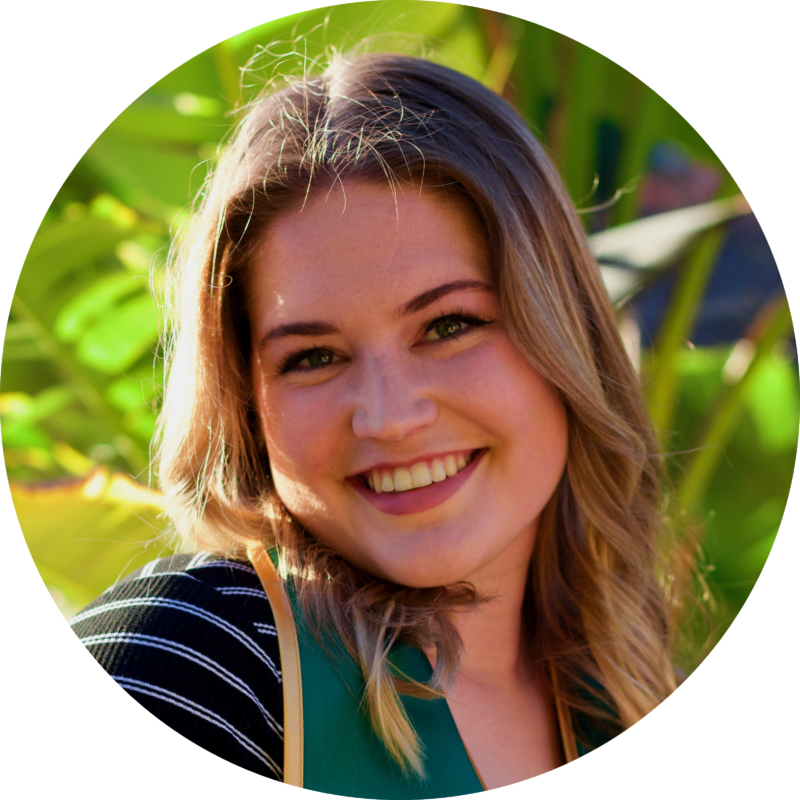
Kelsey Mickelson
Manufacturing Lead
Kelsey utilized her experience as a manufacturing concentration to develop and oversee the build of the sample container dispensing device. Kelsey is originally from Lompoc, CA, and was active at the Innovation Sandbox and SLM research at Cal Poly.
Kelsey has accepted a position at Lawrence Livermore National Labs in Livermore, CA as a mechanical engineer.
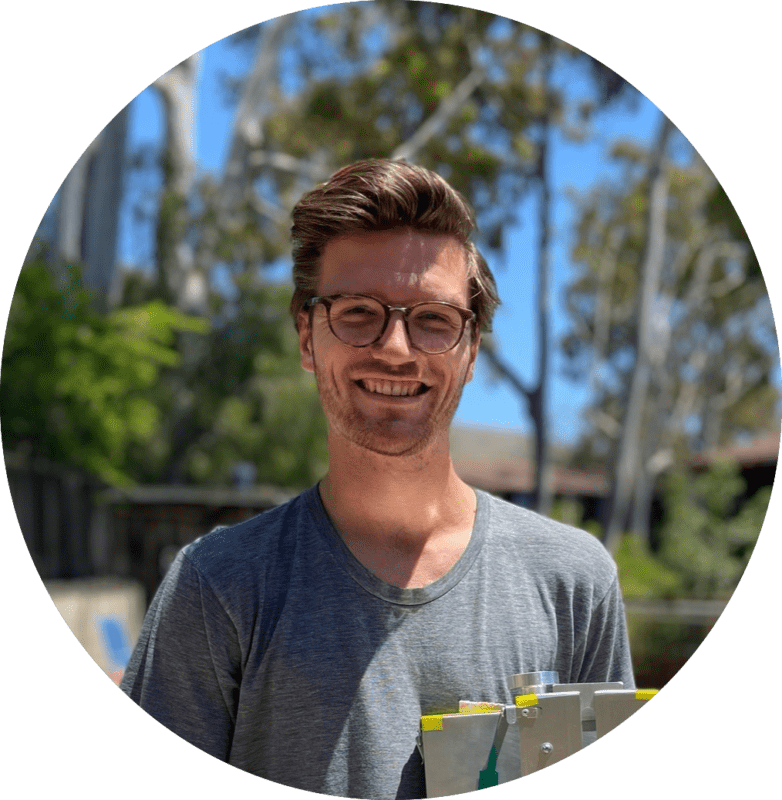
Oscar Popravka
Design lead
Oscar led the design process for this device from the ideation and prototyping phases, to maintaining and updating the detailed CAD assembly. Oscar is originally from San Francisco, CA.
After graduation, Oscar is planning to move back to the Bay Area and pursue a career in mechanical design. He hopes to one day work in the space industry, helping NASA on their future missions to the Moon and beyond.
Acknowledgements
We are grateful to have had this unique and challenging project experience. We would like to thank our senior project advisor, Dr. Mohammad Noori, for his guidance and support throughout the project.
Thank you to the Micro-g NExT staff and technical partners who developed this challenge, provided financial support, and created opportunities to learn from experienced NASA personnel.
Finally, thank you to our NASA mentor, Heidi Hammerstein, who utilized her expertise as a systems engineer and Project PoSSUM Astronaut Candidate to provide invaluable feedback, insight and support.
Project Videos
The following videos provide an overview of our device and footage of our underwater testing.
M.O.O.D. Digital Poster
Background
Micro-g NExT Challenge #3
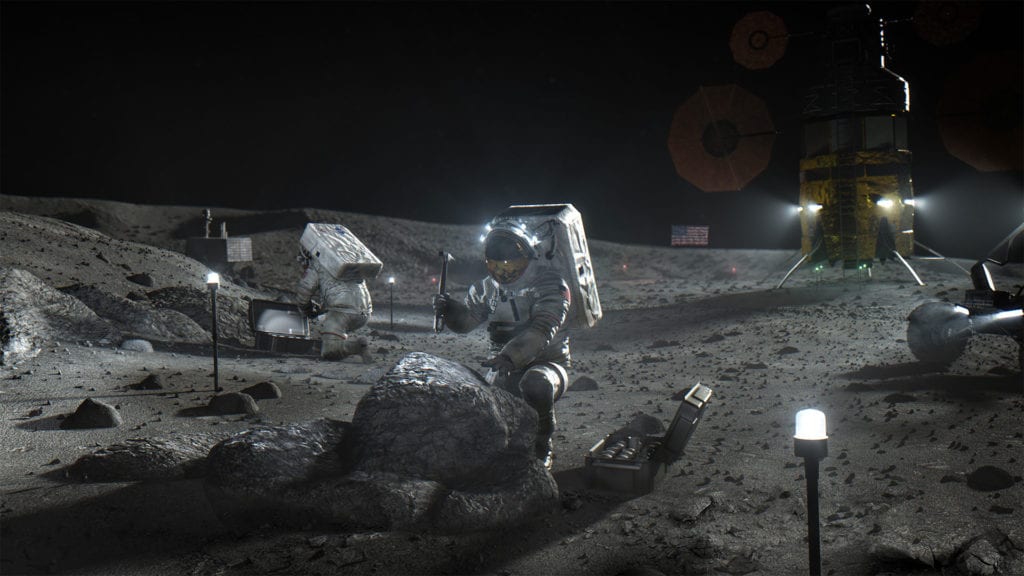
NASA aims to bring the first woman and next man to the moon through the Artemis missions in 2024. The Micro-g NExT program challenges undergraduate students to design, build and test a tool which supports current space exploration challenges. Selected designs are tested by NASA divers in the Neutral Buoyancy Laboratory (NBL) at Johnson Space Center.
Our project targets the 2021 Micro-g NExT Challenge 3, focusing on tools to support the extensive geological sampling which will be conducted during the Artemis missions.
Problem Statement
Astronauts in the Artemis program will collect lunar geological samples to be stored in individual sample bag. Design a sample container dispensing device which astronauts can use with limited dexterity for these sampling operations.
Requirements
Requirements
- Hold 20 sample bags
- Enable one-handed operation for dispensing a single bag
- Prevent bag damage, deformation, and contamination
- Hold up to 2 lbs. sample in bag
- Use only manual power
- Fit within volume of 12″x12″x5″
- Include 4-hole bolt pattern for interface with utility belt
- Operable with EVA gloved hands
- Total dispenser weight should be less than 3 lbs
- Prevent entrapment of fingers
- Aluminum 6061 or 7075, Stainless Steel, and Teflon only
- No sharp edges
- Minimize and label pinch points
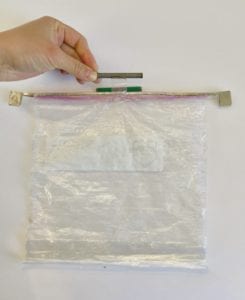
Prototype sample bag with deformable aluminum rim. Design proposal includes sample bag modification to include two aluminum rods on the central teflon tabs.
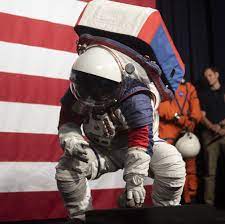
The new xEMU Space Suit has improved mobility, though Astronauts still have limited dexterity and fine motor skills. This necessitates a design that is easy to use with one hand.
Analysis and Design
design process
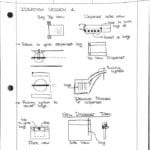
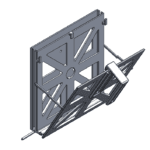
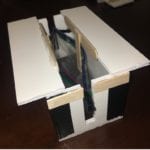
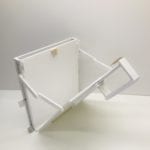
Iterative Design Process: Began with ideation through sketches and rough prototypes. Continually refined design based on background research and feedback from Micro-g NExT experiences and mentor, Heidi Hammerstein.
Analysis
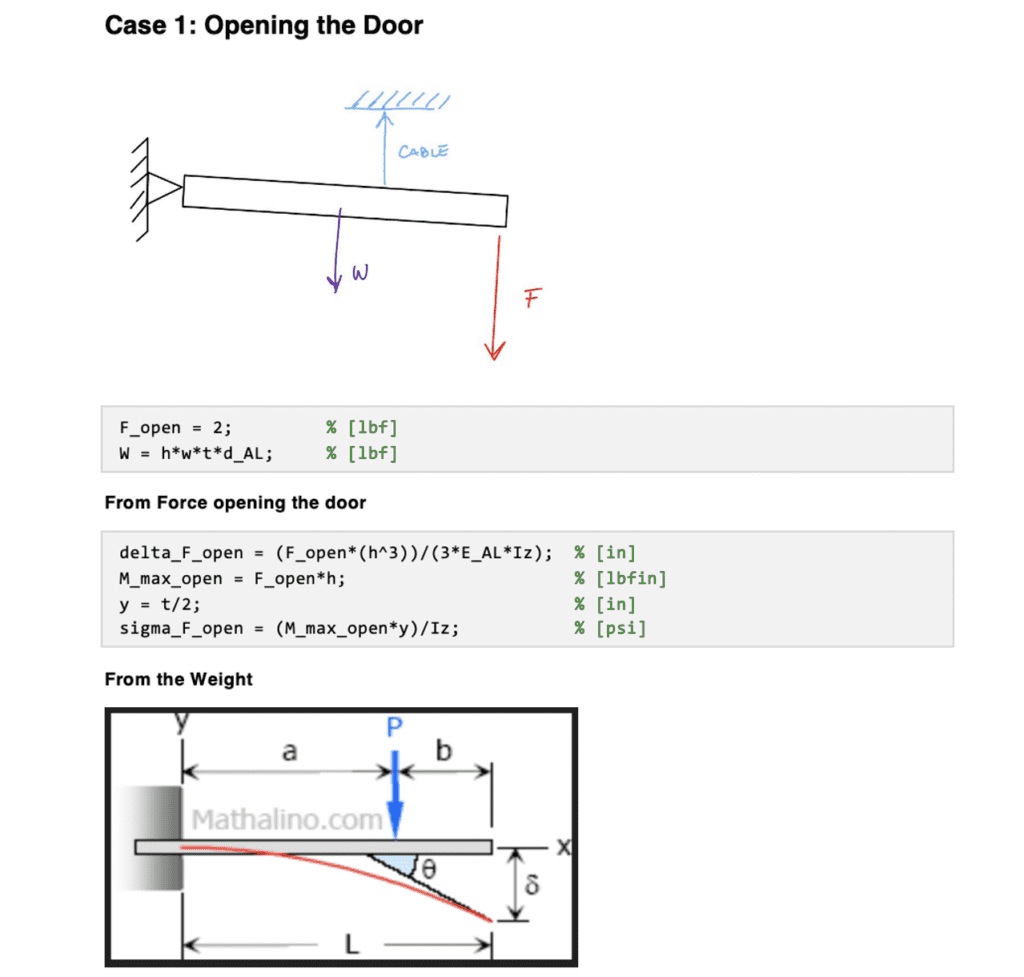
Structural Analysis: Ensure structural stability for nominal load cases, as outlined by challenge technical partners.
Design for Manufacturing: Planned to manufacture in-house. Strict materials requirements created challenges due to limitations in machining capability and material performance.
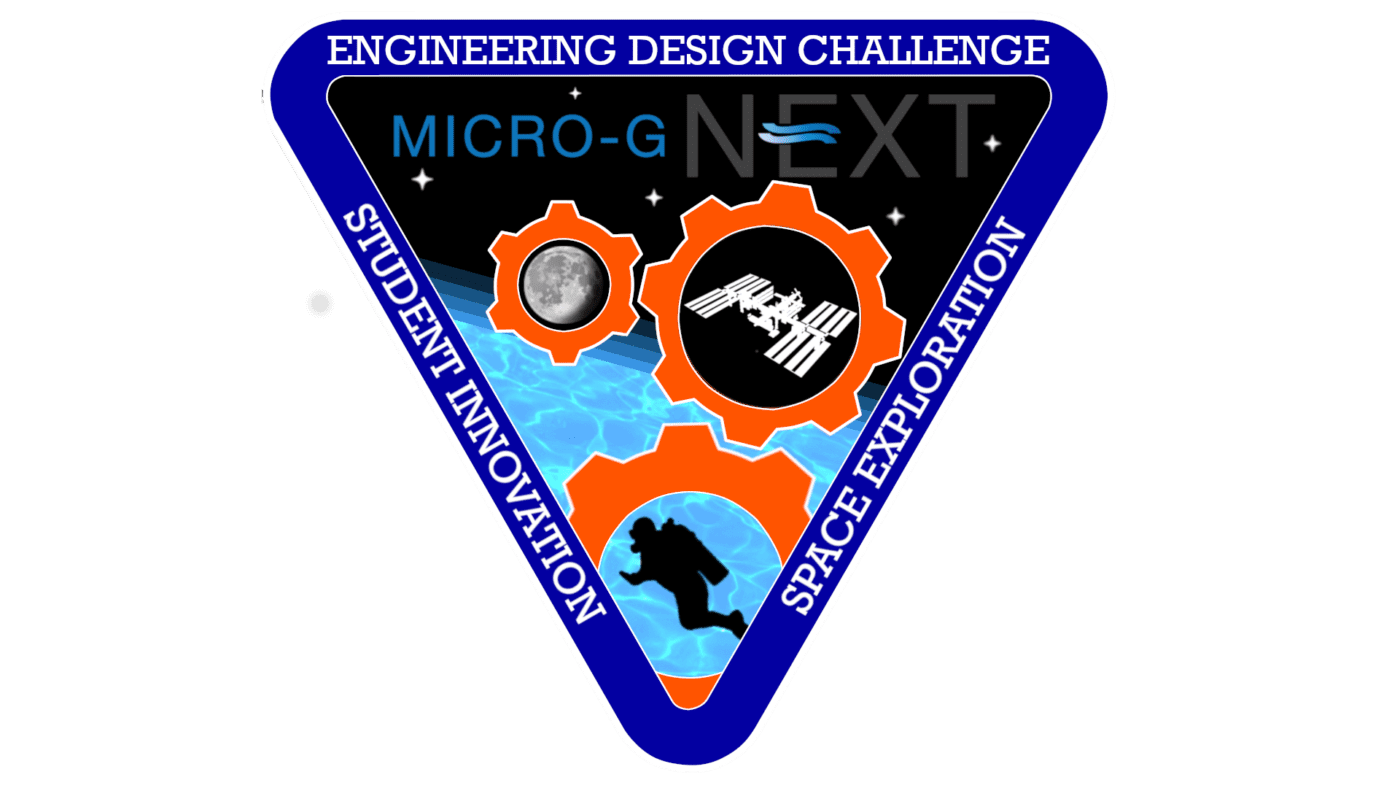
NASA Micro-g NExT
This project is sponsored by the NASA Microgravity Neutral Buoyancy Experiment Design Teams program.
Design Concept
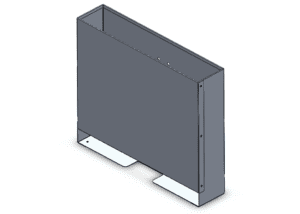
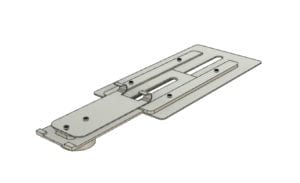

M.O.O.D. Design Description
Our final design concept focused on the one-handed ease-of-use requirement. For this reason, we chose the name “MOOD” for our design – the Micro-g NExT One-Handed Operational Device. MOOD has three main subassemblies:
Bag Container
- Enclosed design: all bags are stored internally until sampling.
- Container has four-hole bolt pattern for mounting to the utility belt.
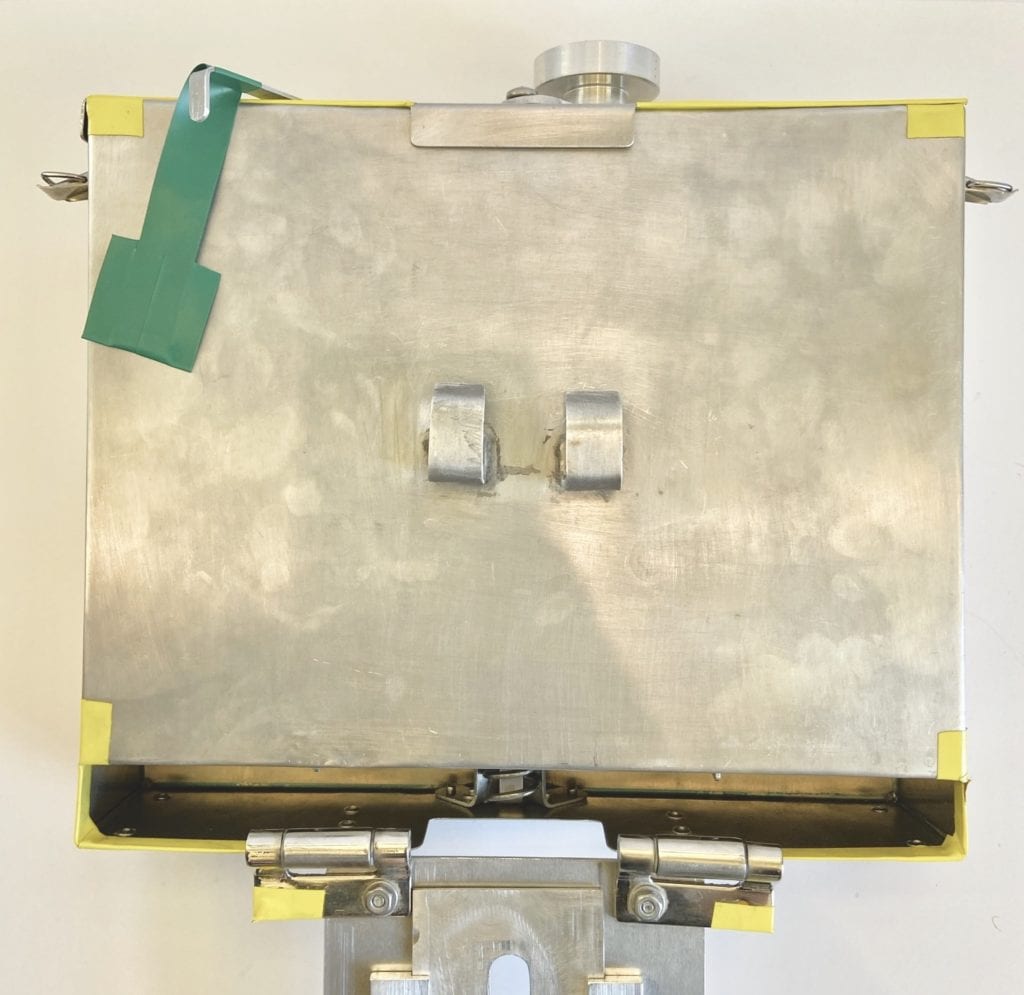
Coil Assembly
- Large, tactile crank handle for EVA-gloved operation.
- Coil and alignment rails allow rolled bag to translate vertically when crank handle is turned.
- Crank turned until bag drops to bottom of bag container.
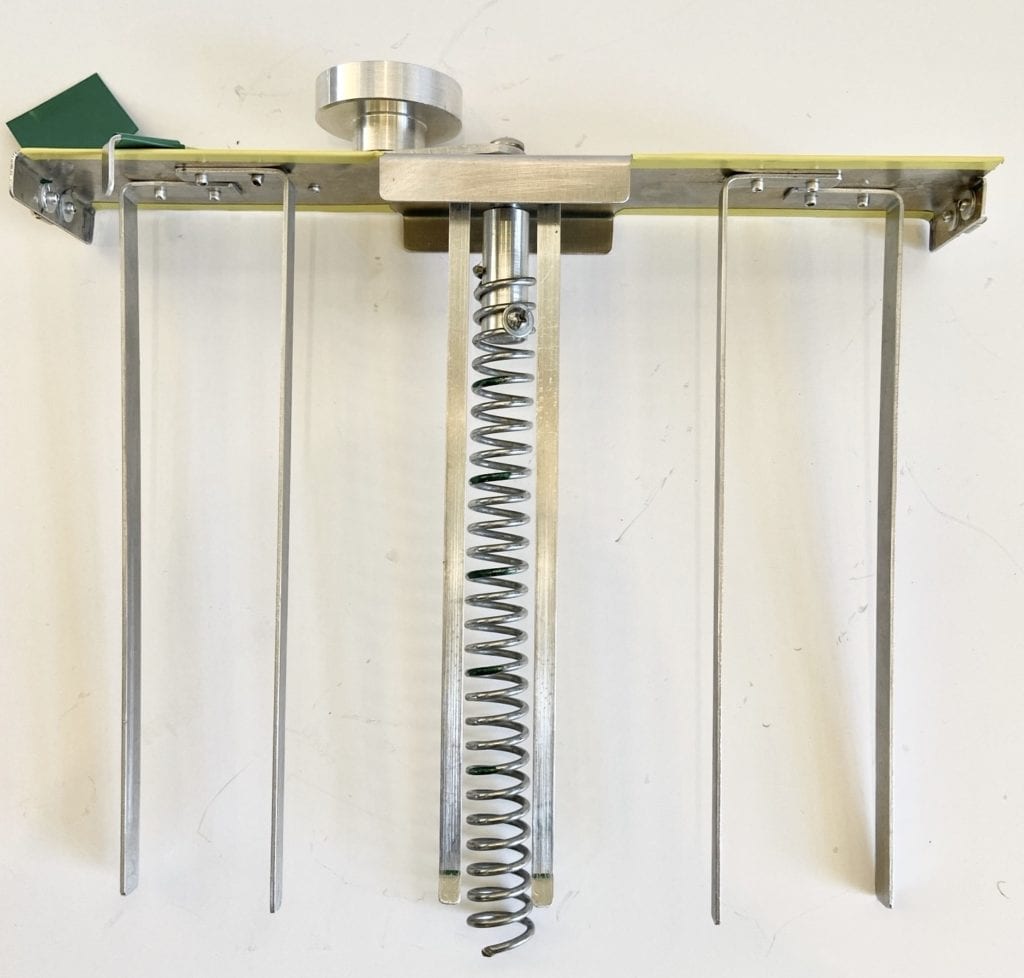
Door
- Three-part extending door: door, sliding panel, hook panel.
- Large, tactile door knob for slider operation.
- Hook panel grabs rods on bag to pull bag up and out of bag container.
- Two degrees of freedom: rotational and translational.
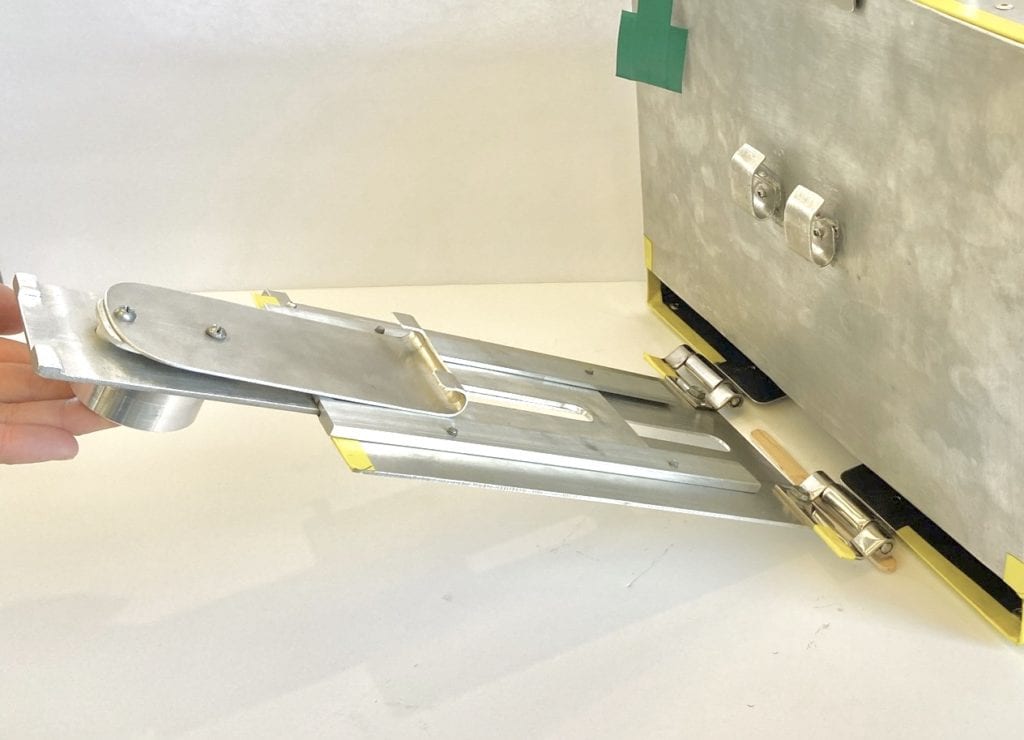
Manufacturing
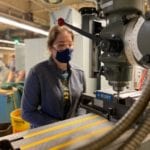
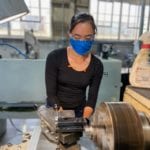
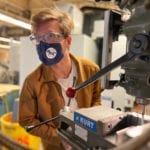
Manufacturing was completed at Cal Poly’s Mustang ’60 and Hangar Machine Shops. Several components utilized water jet cutter, sheet metal bending techniques, and mill and lathe work.
Custom Components
- Bag container and lid
- Coil holder
- Crank arm, handle
- Alignment features
- Door panel
- Slider guides
- Sliding door panel
- Door knob
- Sliding hook panel
- Container hooks
Stock Components
- Coil
- Hinges
- Draw latches
- Fasteners
Testing and Analysis
Specifications
Weight: 2 lbs 14.35 oz
Overall Dimensions: 12″ x 11.75″ x 4.25″
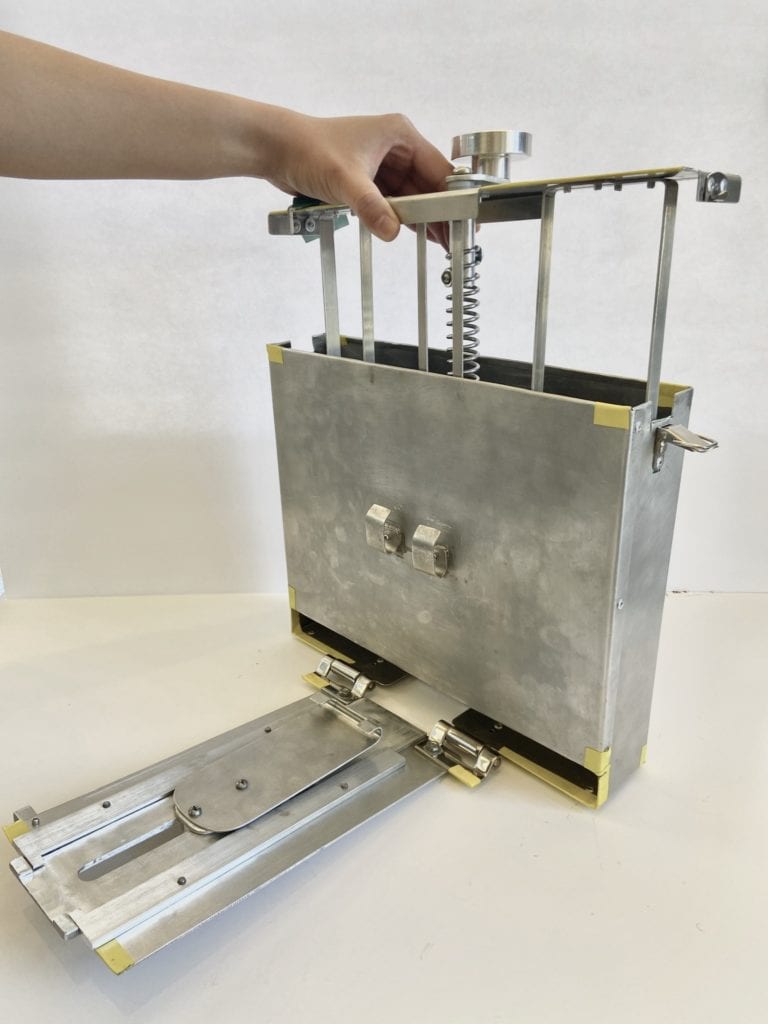
Inspections
Inspections were essential to ensure compliance with the challenge requirements and safety expectations.
Physical Characteristics: Device passed the overall size and weight requirements.
Safety: Device used many design features (fillets, sheet metal hems) to minimize hazards. Remaining hazards labelled in yellow to indicate areas where the divers should exercise caution during testing.
Terrestrial Testing
We first conducted testing in a “terrestrial” environment: under Earth’s gravity in standard atmosphere.
Mechanical Functionality: This testing provided an initial understanding of how the mechanisms performed. However, we soon moved onto underwater testing since MOOD is to be tested in NASA’s Neutral Buoyancy Lab (NBL) as part of the Micro-g NExT program.
Underwater Testing
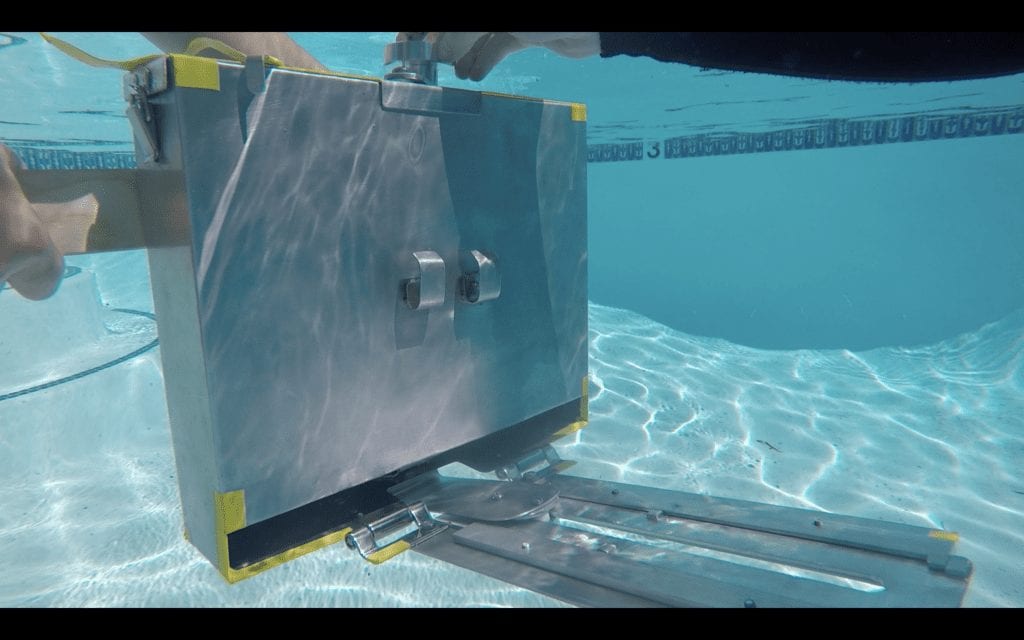
With access to a community pool, we conducted 12 underwater tests over a period of 14 days in preparation for MOOD being sent to the NBL for official testing.
Testing Analogs: In order to simulate the NBL testing environment, we utilized a mock-up arm to which the device is mounted, as well as large gloves for the user to simulate the EVA suit.
Data Collection and Analysis: All of our underwater testing footage was captured with a GoPro camera. Each test had the objective of testing the three main functions of MOOD: the dispensing of the bag, grabbing the first bag rod, then placing the second bag rod. For each round (a full cycle of operations with one bag), we tracked whether these actions were completed successfully (Pass/Fail) and noted any observations.
Iteration: After each testing session, changes were implemented. This iterative process improved the device performance.
Next Steps
Micro-g NExT Virtual Test Week: June 14-16, 2021. The device will be undergo testing at the Neutral Buoyancy Lab by NASA divers. Our team will communicate to the divers via the Test Command Center remotely during the test to provide instruction and receive feedback.
The Virtual Test Week will be streamed live for public viewing.
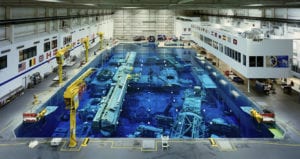
The Neutral Buoyancy Lab is located at Johnson Space Center in Houston, TX. It is 200 feet long, 100 feet wide, and 40 feet deep.
Conclusions and Recommendations
Conclusions
We successfully completed the design, build and test cycle for the sample container dispensing device. In the end, we were able to send off a design which worked efficiently and accurately. This was the result of a lot of rigorous work, but also a lot of testing and observations which enabled us to improve our design day by day. This project highlighted the importance of design-for-manufacturing and iterative testing.
Recommendations
- Add features to improve operation with limited visibility
- Further reduce weight
- Expand testing to volunteer users to obtain additional ease-of-use feedback
Micro-g NExT Community Outreach
Our team conducted community outreach to fulfill a Micro-g NExT challenge requirement. We conducted four guest high school science lessons at San Luis Obispo Classical Academy. These lessons covered 9th grade earth science and 12th grade physics topics, connecting the students’ curriculum to our Micro-g NExT project and NASA’s research and missions.